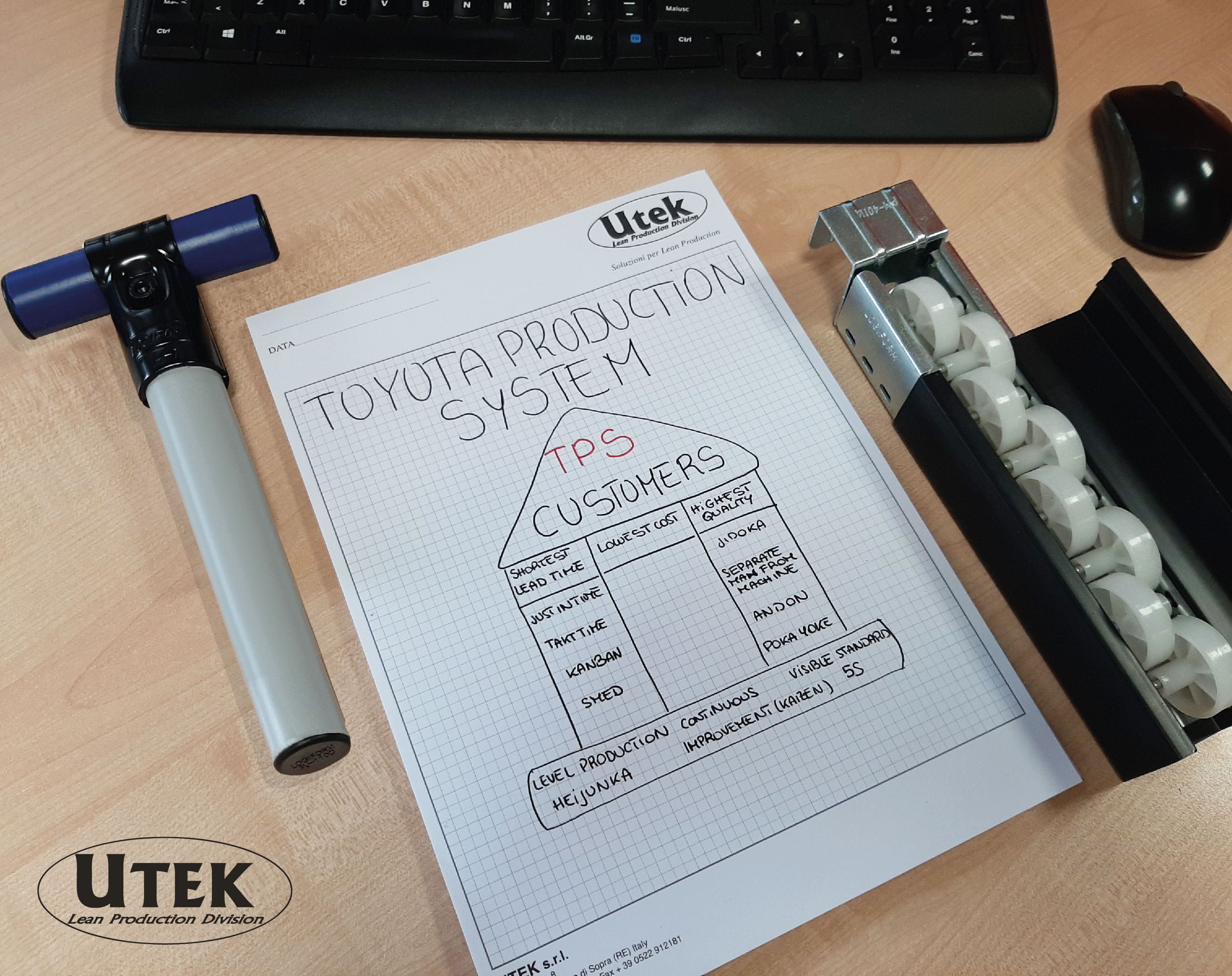
Toyota Production System (TPS), questa sigla ti sembrerà nota se hai conoscenza dei processi di Lean Organization, logistica e gestione dei flussi aziendali. Il motivo: quando parliamo di TPS ci riferiamo a strategie pensate per semplificare e snellire i processi interni.
Siamo sempre alla ricerca di nuovi sistemi per ridurre le frizioni, lavoriamo con tecniche di Lean Production e Six Sigma per fare in modo che ogni dettaglio sia ottimizzato.
Toyota Production System TPS, cos'è e a cosa serve?
Toyota Production System o più comunemente TPS è una strategia ideata all’interno della casa automobilistica giapponese Toyota con l'obiettivo di snellire l’organizzazione logistica e produttiva di un’azienda sfruttando in maniera produttiva le risorse già disponibili.
I punti di forza che la contraddistinguono sono:
- La stretta relazione di collaborazione che si crea tra la parte operativa e dirigenziale dell’azienda
- Focus sulla qualità come obiettivo primario
- Ricerca continua di miglioramento
- Risposta attiva e coerente alle richieste del mercato
- Riduzione al minimo delle scorte a magazzino
Per comprendere il pensiero alla base Toyota Production System TPS è necessario fare un passo indietro fino alla fondazione dell’azienda Toyota.
TPS, storia del sistema di produzione Toyota
La società viene fondata nel 1890 da Sakichi Toyoda con il nome di Toyoda Automatic Loom, azienda produttrice di telai tessili. La variazione del cognome del fondatore è frutto di pensiero scaramantico in quanto Toyota a differenza di Toyoda, poteva essere scritto in Giapponese con 8 colpi di pennello, numero considerato fortunato nel Giappone dell’epoca.
Solo nel 1933 venne aperta una divisione dedicata alla produzione di automobili la quale venne affidata al figlio Kiichiro Toyoda.
Dobbiamo però aspettare fino al 1937 perché tale divisione venga tramutata in società indipendente, diventando così la Toyota Motor Company, passaggio avvenuto sotto pressione del governo per la crescente necessità di autocarri per l’esercito imperiale Giapponese durante la Seconda Guerra Mondiale.
L’allontanamento effettivo dal modello fordista avviene però nel dopoguerra quando le poche risorse non permettevano di abbracciare una produzione di massa per abbattere i costi, nonché a seguito dei frequenti viaggi negli Stati Uniti di Taiichi Ohno, allora membro del consiglio esecutivo della compagnia, il modello Ford Motor inizia a essere visto negativamente perché ritenuto pieno di “Muda” ovvero sprechi.
Se le visite alle aziende basate sul modello fordista sono un “flop” agli occhi di Taiichi Ohno, la scoperta dei negozi della catena di supermercati Piggly Wiggy, segna la svolta. Questi supermercati usavano una tecnica di allestimento dei prodotti per la quale eri costretto a seguire un determinato percorso lungo il quale trovavi la merce sulle scaffalature pronta per essere prelevata e portata alla cassa per pagare.
Taiichi Ohno decide pertanto di prendere spunto da questa tecnica di allestimento per ripensare l’organizzazione interna di Toyota promuovendo una produzione strettamente collegata all’andamento della domanda del mercato, direzione diametralmente opposta al pensiero Fordista (produrre di più per stimolare l’offerta).
Nasce così il Toyotismo o come verrà denominato in fase di elaborazione da tra il 1948 e il 1975, Toyota Production System (TPS).
TPS è attualmente riconosciuto come precursore dello sviluppo dei concetti e principi della produzione snella.
I principi del Toyota Production System
Conoscere il pensiero alla base di TPS spinge molte aziende a decidere d’intraprendere un percorso di miglioramento e rivoluzione aziendale.
Impariamo dunque quali sono i 14 principi utilizzati da questo sistema:
- Implementare un metodo di pensiero a lungo termine
- Sviluppare un work-flow il più possibile costante e continuo
- Evitare di produrre più di quanto richiesto dal mercato, ovvero seguire una logica di tipo “Pull” e “Just in Time”; produrre solo ciò che è stato ordinato, nel momento in cui viene richiesto.
- Livellare il carico di lavoro per evitare momenti di stallo o di accumulo di lavoro, questo concetto può essere riassunto con il termine “Heijunka” che appunto è un metodo per livellare la produzione ed evitare oscillazioni in eccesso o difetto.
- Costruire una cultura aziendale proattiva ovvero indirizzata all’individuazione e risoluzione delle problematiche in maniera tempestiva.
- Promuovere la gestione e organizzazione visiva degli spazi affinché tutti siano sempre informati e in maniera immediata riguardo a procedure, cambiamenti, situazioni di pericolo, norme da rispettare ecc…
- Implementare solo tecnologie a supporto dell’attività umana e non in sostituzione
- Promuovere la comunicazione della filosofia TPS dai leader ai dipendenti
- Investire sulle persone per creare team di lavoro efficienti e stabili
- Promuovere i rapporti con i fornitori per creare una rete di supporto al proprio business, solida e sicura
- Osservare e parlare con chi lavora attivamente nell’azienda per individuare opportunità di miglioramento, anche questo principio si riassume con il termine “Gemba”.
- Ogni decisione deve essere prima valutata e discussa con più membri del team aziendale affinché venga presa in maniera ponderata e rispettando il volere della maggioranza
- Sfruttare tutte le tecniche utili all’azienda per poter rispecchiare la continua ricerca di miglioramento
Applicare il Toyota Production System
Il successo del Toyota Production System risiede proprio nel suo volersi distaccare dalle leggi che regolano solitamente il mercato, strettamente legate al profitto e alla produzione di massa.
Se molte aziende puntarono e focalizzano tutt’ora il proprio sviluppo sull’implementazione di novità tecnologiche per Toyota non è mai stata una precorritrice in questo ambito, piuttosto ha seguito questo sviluppo incorporando ciò che di utile poteva trarne.
Toyota in ambito automobilistico ha prodotto veicoli che si distinguevano grazie alla loro affidabilità e qualità, riuscendo a rispondere sempre attivamente alle richieste mutevoli del mercato senza rischiare di legarsi o peggio fossilizzarsi su determinati prodotti a causa di accumuli di scorte o aumento dei costi.