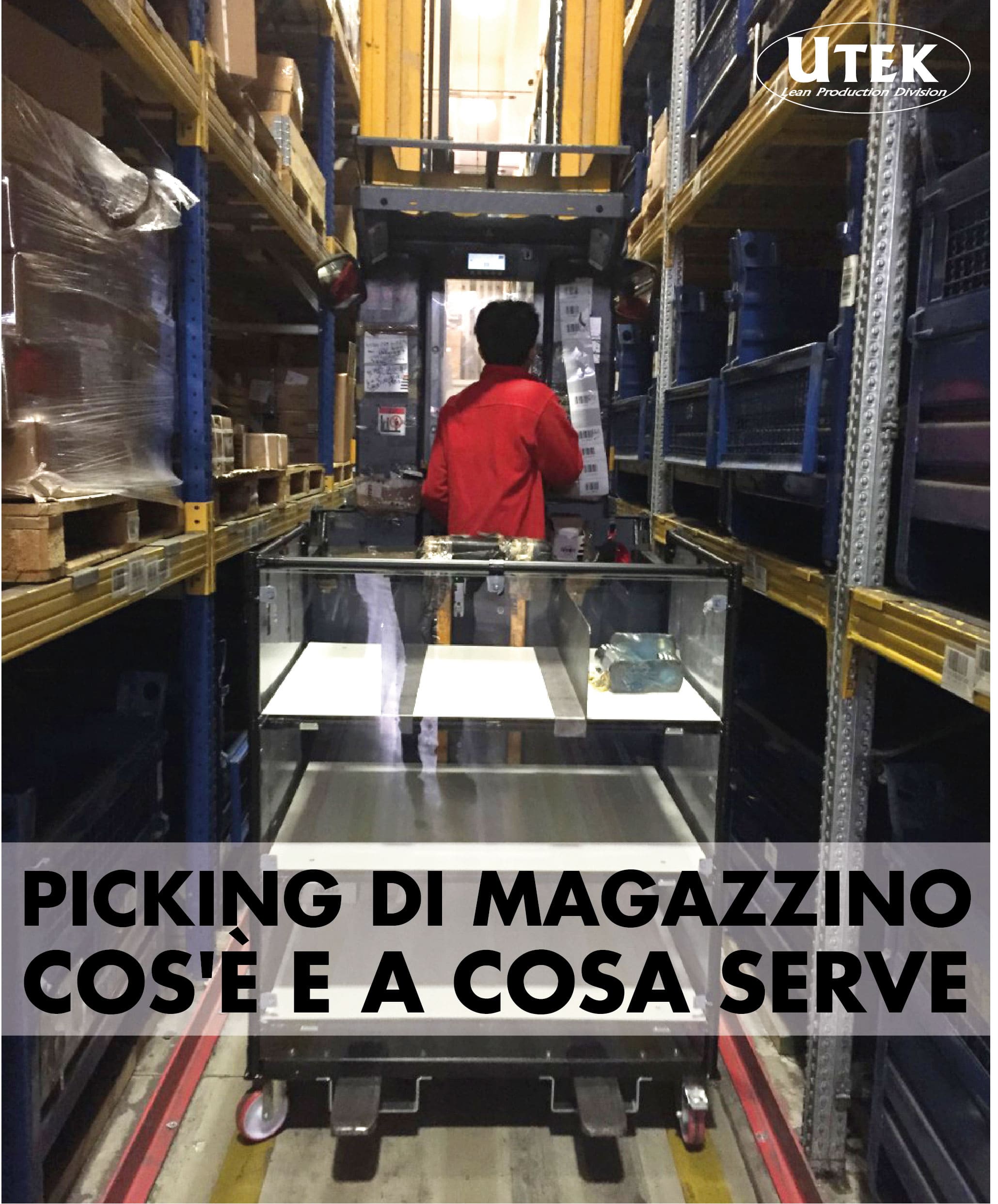
Il picking di magazzino è un'attività che mette a dura prova la tua capacità organizzativa in azienda. La logistica è al centro delle tue attenzioni ma anche quello che accade nell'area di stoccaggio dovrebbe essere preso in considerazione se vuoi ottimizzare i tempi, gli spazi, i costi e gli sprechi. Questo è il lavoro da affrontare se vuoi lavorare in termini di lean production.
Ovvero se vuoi gestire ogni aspetto della tua azienda misurando, ottimizzando, migliorando costantemente per eliminare gli sprechi e raggiungere la perfezione. L'area di conservazione delle materie prime e della merce è uno dei nodi più difficili da risolvere, per questo è giusto affrontare in questa sede il tema del picking di magazzino. Sai di cosa stiamo parlando?
Picking di magazzino, una definizione
Con questo termine intendiamo tutto il lavoro di gestione dell'oggetto in termini di prelievo, smistamento e suddivisione di materiale da una tipologia di carico a diverse altre.
L’attività di picking è estremamente importante per una gestione efficiente del magazzino.
Il picking di magazzino rientra nel ciclo di approvvigionamento delle scorte, alle operazioni di spedizione e alla preparazione degli ordini.
Se ci sono carenze, errori o ritardi, tutta la catena produttiva ne risente, non solo, anche a livello finanziario è giusto sottolineare come i costi legati al picking si aggirano attorno al 60% del bilancio totale, aspetto che ricorda a tutte le aziende quanto sia fondamentale investire nell’ottimizzazione delle procedure di picking.
Queste si basano su operatori formati, capaci e motivati, layout di magazzino sviluppati appositamente per snellire le attività, sistemi e strutture di stoccaggio adeguati alla tipologia di prelievo e tecnologie sempre all’avanguardia con le esigenze produttive.
Quanti tipi di picking di magazzino esistono?
Nonostante esistano numerose variabili connesse all’attività di picking, possiamo ugualmente cercare di definire una serie di tipologie che riassumono a grandi linee le tecniche più comuni:
- Picking a zone: Tecnica utilizzata quando gli ordini sono multi componente, pertanto anche il magazzino viene idealmente suddiviso in aree dove un operatore per postazione, si occupa di prelevare, preparare e disporre in un “contenitore” un componente. Questa box viene poi fatta scorrere lungo tutte le postazioni fino al completamento dell’ordine.
- Prelievo di base: E’ il metodo di prelievo più semplice dove un operatore al quale è stato dato un ordine da preparare, gira per il magazzino per prelevare tutti i componenti e disporli in un contenitore per la spedizione. In questi casi solitamente, per snellire l’operazione di ricerca per l’operatore, viene preparata una “mappa” con il percorso da seguire per il prelievo di tutte le parti.
- Prelievo multi ordine: Questa tecnica ottimizza la preparazione di più ordini con i medesimi componenti, infatti il picker parte con una lista di ordini da preparare e tramite codice a barre, preleva di ogni pezzo un numero pari alla somma di quelli necessari per ogni commessa dell’elenco. Alla fine si reca in un’area di smistamento dove suddivide i componenti per ordine e li prepara per la spedizione.
- Cluster picking: Si tratta sempre di un prelievo multi ordine che però prevede che il picker faccia un unico giro nel magazzino prelevando contemporaneamente più ordini e disponga i pezzi già suddivisi dentro a contenitori adibiti. In questo modo a fine attività gli ordini sono pronti per la spedizione senza ulteriori manipolazioni.
- Prelievo a onde: Questa tecnica prende il nome dalla cadenza ritmata dell’attività di prelievo. Ogni giorno viene pianificata la scaletta giornaliera degli ordini che devono essere preparati in determinati momenti della giornata per ottimizzare le operazioni di prelievo.
- Pick to belt: Questa tipologia di prelievo si applica ai prodotti pre-imballlati, solitamente quelli di dimensioni grandi o parte di assiemi, che una volta ordinati, vengono estratti a magazzino e condotti direttamente all’area spedizioni.
Quali sono le principali strategie di picking?
Le strategie maggiormente utilizzate sono:
- Man-to-goods: Addetto al picking che si muove nel magazzino alla ricerca del materiale da prelevare;
- Goods-to-man: I prodotti vengono fatti arrivare alla postazione del picker per essere smistati, imballati e spediti;
- Modello ibrido: E’ un sistema misto dove il magazzino è in parte automatizzato e software gestionali dialogano con il lavoro dell’operatore.
Nel concetto più classico di attività di picking Man-to-goods è l’operatore a cercare i prodotti a magazzino e per farlo ha bisogno di un layout degli stock pensato per favorirne un’efficiente e veloce fruizione. In questi casi si opera per un'organizzazione logica dei vari elementi considerando che si devono sfruttare tutte le misure.
Anche quelle in altezza sfruttando magazzini verticali. Quindi le merci a bassa rotazione (che non vengono utilizzate spesso) e più voluminose si trovano nei punti più alti e difficili da raggiungere e quelle più piccole, facilmente prelevabili, ad altezza uomo, ancora meglio se disposte su scaffalature a gravità FIFO in grado di favorire un prelievo semplice, veloce e senza rischio d’invecchiamento dei materiali.
Soprattutto quando si lavora su grandi superfici. Di conseguenza entra in gioco il picking di magazzino che contempla strategie, tecniche e strumentazione per velocizzare i processi. In primo luogo si utilizzano le tecnologie di radiofrequenza, barcode e picking vocale.
Questo passaggio consente di eliminare documentazione cartacea e burocratizzazione della logistica. Poi si procede con scaffalature leggere, modulabili e basate sul principio dello scorrimento. Si sfrutta la gravità per fare in modo che sia l'oggetto ad arrivare all'operatore.
Picking in base al layout di magazzino
Imparare a disporre le merci a magazzino per facilitare le attività di picking è un aspetto importante che non va sottovalutato ma è giusto ricordare che la struttura è quella che delinea la tipologia di attività di picking più adatta da seguire.
Il layout lineare è quello scelto per i magazzini con spazi esterni ampi e nei quali pertanto le merci possono viaggiare in un unico senso e l’attività di picking segue in successione quella dello stoccaggio.
Il layout a “U”, adottato negli ambienti con spazi esterni ridotti, prevede aree di carico e scarico affiancate, pertanto l’attività di picking va a snodarsi internamente a queste aree.
Il layout a “L” infine è anch’esso legato ad ambienti con spazi esterni ridotti dove le aree di ricevimento e spedizione sono ai poli opposti del magazzino e le operazioni di picking vengono gestite nel mezzo per snellire il passaggio dei prodotti dall’entrata all’uscita.
Addetto al Picking: Chi è, funzioni e ruolo
L’addetto al picking o picker (in inglese) è un operatore formato e specializzato del settore della logistica, responsabile del prelievo e raggruppamento dei materiali necessari all’evasione di un ordine. Il suo compito non si limita a un’attività di sola movimentazione dei prodotti, deve anche occuparsi del controllo qualità, delle scorte e del trasporto della merce fino all’area di spedizione.
L’introduzione di nuove tecnologie hanno reso questo ruolo differente a seconda dell’organizzazione aziendale e del tipo di settore. Non per forza è l’operatore a dover andare dai prodotti, spesso e volentieri ormai sono questi che vengono condotti alla postazione del picker. Nel tentativo di snellire e velocizzare tale procedura sono state sviluppate molte tecniche di prelievo innovative che sfruttano software gestionali, strutture a gravità FIFO, sistemi pick to light, carrelli e mezzi semi automatici per il trasporto dei materiali e così via.
Prima di parlare delle varie tipologie e tecniche di picking è giusto fare un passo indietro e completare il profilo del picker, elencandone le funzioni aziendali:
- Deve raggruppare tutte le parti di un ordine e consolidare
- In una postazione apposita deve imballare e etichettare tutte le parti dell’ordine
- Se si tratta di volumi piccoli, solitamente il nostro addetto al picking ha anche il compito di stilare la documentazione necessaria per completare e rendere valido l’ordine. In caso di flussi più importanti di materiale, software appositi snelliscono tale operazione.
- Deve anche gestire l’approvvigionamento delle scorte, o manualmente o tramite sistemi di gestione automatica o semi-automatica degli stock a magazzino.
Il picker è un profilo professionale in continuo aumento grazie soprattutto alla crescente popolarità degli e-commerce.
La preparazione degli ordini è parte di qualunque organizzazione logistica, le aziende ricercano continuamente figure da inserire nel loro organico, in grado di sapersi destreggiare abilmente tra diverse attività, mantenendo un crescente grado di efficienza e produttività. Una caratteristica fondamentale per un addetto al picking è la flessibilità, questo perché tutta la formazione necessaria non è sufficiente. Ogni ambiente produttivo ha la possibilità di decidere la propria formula per la gestione delle operazioni di picking, pertanto è necessario sapersi destreggiare tra gestioni manuali, semiautomatiche e automatiche.
Le attività di picking per grandi volumi necessitano di formazione per l’uso di transpallet e carrelli elevatori, invece quando la varietà di prodotti è il punto cruciale, è importante saper utilizzare scanner per codici a barre e terminali a radiofrequenze.
Le nuove tecnologie affiancano e supportano il profilo dell’addetto al picking nell’evitare errori e ritardi nelle consegne, caratteristica che rende competitiva o meno un’azienda, agli occhi di clienti, fornitori e del mercato in generale.
Come migliorare il picking di magazzino?
L'obiettivo principale di ogni attività di picking è quello di ridurre al minimo il tempo che intercorre tra la ricezione dell’ordine e la partenza del materiale pronto.
Al di là della tipologia di picking che si decide di adottare per la propria attività, è importante tenere a mente alcuni aspetti fondamentali per una migliore gestione del magazzino:
- Gestione delle attività di picking da entrambi i lati della corsia per una facile fruizione
- Evitare corridoi chiusi che impediscono di circolare più facilmente e velocemente, tra le corsie
- Posizionare i materiali meno richiesti nei corridoi più esterni e di minor passaggio
- Preferire un giro solo per più ordini in modo da limitare i viaggi e ottimizzare i tempi di gestione degli ordini.
Questi suggerimenti su una gestione efficiente delle attività di picking, dimostrano come non esista una tecnica di picking più funzionale di altre, la scelta dipende da innumerevoli fattori quali: Gli spazi che si hanno a disposizione, la distribuzione degli stock a magazzino, dei materiali e la struttura degli ordini.
Tutto questo può essere gestito con l'attrezzatura Utek che permette di organizzare scaffalature con relative etichette visive per semplificare il lavoro. Con il sistema modulare Utek è possibile creare qualsiasi tipo di struttura secondo le proprie esigenze. Per maggiori informazioni è possibile contattarci all'indirizzo di posta elettronica info@utekvision.com