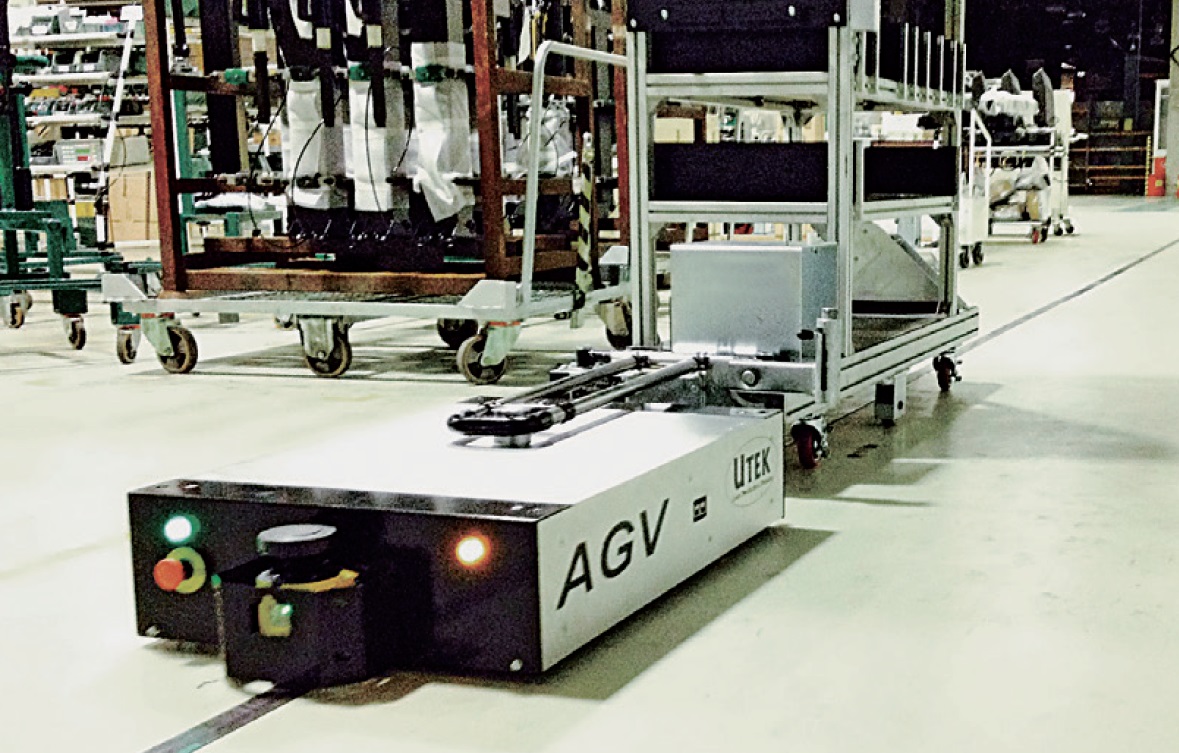
Cos'è il Milk Run (corsa del latte)? In Intralogistica è un metodo di consegna delle scorte e delle materie prime tra il magazzino e le linee di produzione. Il sistema Milk Run è solitamente un trasporto in-plant.
Indice dei contenuti
- Sistema Milk Run: origine del nome
- Milkrun per la logistica moderna
- Perché usare il sistema Milk Run?
- Quali sono i vantaggi di questa soluzione?
- Come organizzare questo sistema di trasporto?
- Calcoli per il dimensionamento del Milk Run
- Come stimare il tempo ciclo del Milk Run?
- Come dimensionare il Milk Run?
- Come pianificare il layout del Milk Run?
- E nella tua azienda?
Il Milk Run si basa sulla filosofia di PULL, mantenendo basse le scorte e facilitando la fornitura del materiale. Adatto alle produzioni in serie, svolto con filosofia Just In Time, o utilizzato con il Kitting svolge un ruolo chiave nella logistica. È un valido supporto dello SMED, per essere efficienti c’è la necessità di avere ciò che serve.
Assicura una consegna puntuale e riduce la possibilità di sprechi e danni ai materiali. Un punto sempre molto delicato e fondamentale per la Lean Manufacturing è l’ottimizzazione delle scorte e delle materie prime. Il quale sottolinea un punto essenziale: il magazzino deve essere snello. Quindi deve eliminare qualsiasi forma di spreco.
Requisiti di un sistema Milk Run
Regolarità, il Milk Run ha origine in magazzino, si sposta lungo un percorso fisso con più fermate dove sostituisce i contenitori vuoti con i pieni e alla fine ritorna al punto di partenza.
Programmazione, il Milk Run opera quando la linea è in funzione, la corsa inizia e si ripete ad orari prestabiliti.
Come coniugare con la Lean Manufacturing? Bisogna evitare di acquistare materiale e prodotti in eccesso rispetto al fabbisogno del processo produttivo. E il Milk Run aiuta proprio a ottimizzare questo processo grazie a un sistema comprovato e molto utilizzato, basato sul metodo di consegna e ritiro del latte in voga negli Stati Uniti.
Sistema Milk Run: origine del nome
Il concetto della tecnica Milk Run si basa sull'approvvigionamento del latte tipico degli Stati Uniti d'America. A causa della breve durata del latte, il furgone che passa per ogni casa lungo il percorso: ritira le bottiglie vuote e lascia quelle piene. Porta i contenitori vuoti in fattoria e li riempie per consegnarli il giorno dopo.
Questa bottiglia vuota non è per il suo riutilizzo, ma è un segnale visuale per indicare la quantità di latte consumato da approvvigionare. Nel gergo Lean, questa bottiglia è un Kanban! Massima efficienza, minimo spreco: le famiglie hanno solo quello che serve, non ci sono scarti di lavorazione, si annullano gli spostamenti. Il sogno di una vera produzione snella che lavora anche su due concetti fondamentali (fonte Wikipedia):
Far fluire tutte le attività. Tutto deve realizzarsi per processi e non per funzioni, senza soste o interruzioni. Impostare le attività secondo la logica "pull" e non "push", ovvero realizzare un'attività solo quando il processo a valle lo richieda.
Milk Run per la logistica moderna
Il concetto di Milk Run presente nel intralogistica moderna è lo stesso utilizzato per la consegna del latte (tranne per il prodotto). È il metodo per approvvigionare materiale da un magazzino centrale alle linee di assemblaggio.
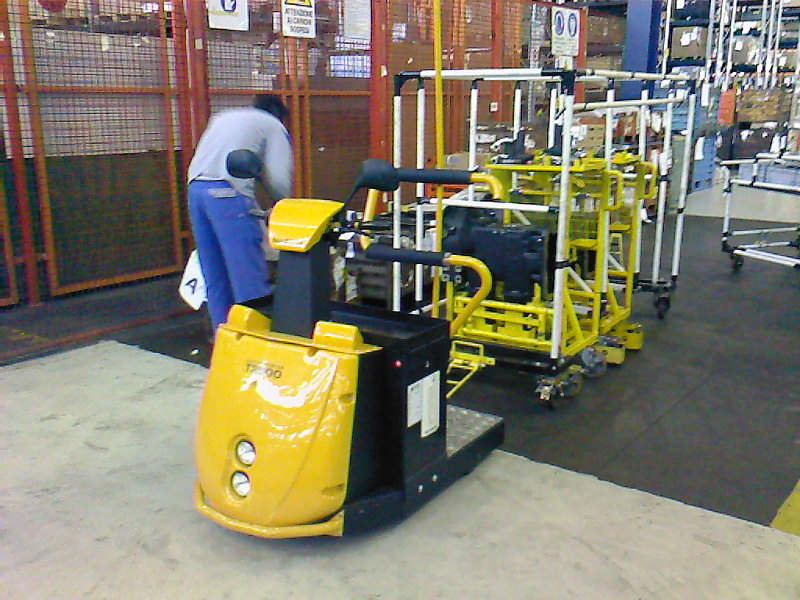
Perché conviene usare il metodo Milk Run? La differenza sostanziale tra il Milk Run e altri sistemi di approvvigionamento sta nelle consegne in piccole quantità, di solo quello che serve per il compito specifico.
Si può realizzare il punto della Lean Production: la fornitura del bene per portare avanti il processo produttivo in chiave snella. Quindi limitando sprechi, scorte inutili e tempi morti. Per produrre nella quantità necessaria (seguendo la logica Just In Time) c'è bisogno di un sistema Milk Run che consenta di ottenere solo ciò che serve.
Quali sono i vantaggi del Milk Run?
Segue la filosofia del Lean Manufacturing, una volta fatta la pianificazione del trasporto diventa uno standard semplice e ciclico che si ripete più volte, un miglioramento rispetto alla chiamata del operatore o del sistema ERP.
Il Milk Run fa parte di una produzione PULL, i contenitori sono i Kanban che vengono riforniti in base al consumo, non c’è accumulo di scorte e i rischi collegati (danni, furti o sprechi). Se il consumo è maggiore il sistema tirerà di più, se c’è inferiore tirerà di meno. Questa modalità di gestione richiede poche risorse dedicate alla pianificazione e fà risparmiare spazio in postazione bilanciando correttamente gli approvvigionamenti del Milk Run.
Semplifica la gestione logistica, caricare basse quantità di materiale aumentando i viaggi può sembrare uno spreco. Ma i piccoli lotti sono meglio gestibili e aumentano il coefficiente di carico del mezzo ottimizzando il viaggio e l’organizzazione della logistica. In questo modo la gestione è unificata e l’approvvigionamento razionalizzato ottenendo una riduzione del ciclo di consegna e un aumento della flessibilità in produzione.
I vantaggi di una gestione Milk Run nell'approvviggionamento aziendale si possono riassumere nella riduzione dei costi di gestione, degli spazi e l'eliminazione dei carrelli elevatori dalle linee. Per un'azienda è essenziale ottimizzare le risorse economiche e coordinare le risorse produttive al fine di migliorare le performance.
Come organizzare il Milk Run?
Hai bisogno di pianificazione nell'approvvigionamento. Innanzitutto devi identificare il tipo di treno. Per la logistica esterna è un camion o un furgone, mentre per la logistica interna può essere un operatore Mizu da “Mizusumashi“ che spinge un carrello o più comunemente che traina un numero di carrelli con un trattore elettrico.
È possibile utilizzare veicoli a guida automatica AGV che consentono di consegnare senza conducente. Per scaricare i contenitori pieni e caricare i vuoti è necessaria la presenza di un operatore o di un sistema Karakuri.
I trattori elettrici trainano carrelli con ripiani per gestire i piccoli contenitori, trolley con pianale per trasportare interi pallet o carrelli dollies per movimentare pile di cassette. Il sistema Milk Run è ottenuto grazie al timone di traino nella parte anteriore del carrello, che crea treni logistici ottimizzati per l'asservimento delle linee.
Queste consegne sono più efficienti se con un treno di carrelli Tugger si lascia direttamente i carrelli o i container presso le postazioni di montaggio. Utilizzando il sistema modulare di logistica Utek composto da profili tubolari lean, giunti e connettori metallici potrai realizzare carrelli e altre applicazioni Lean in Golden Zone.
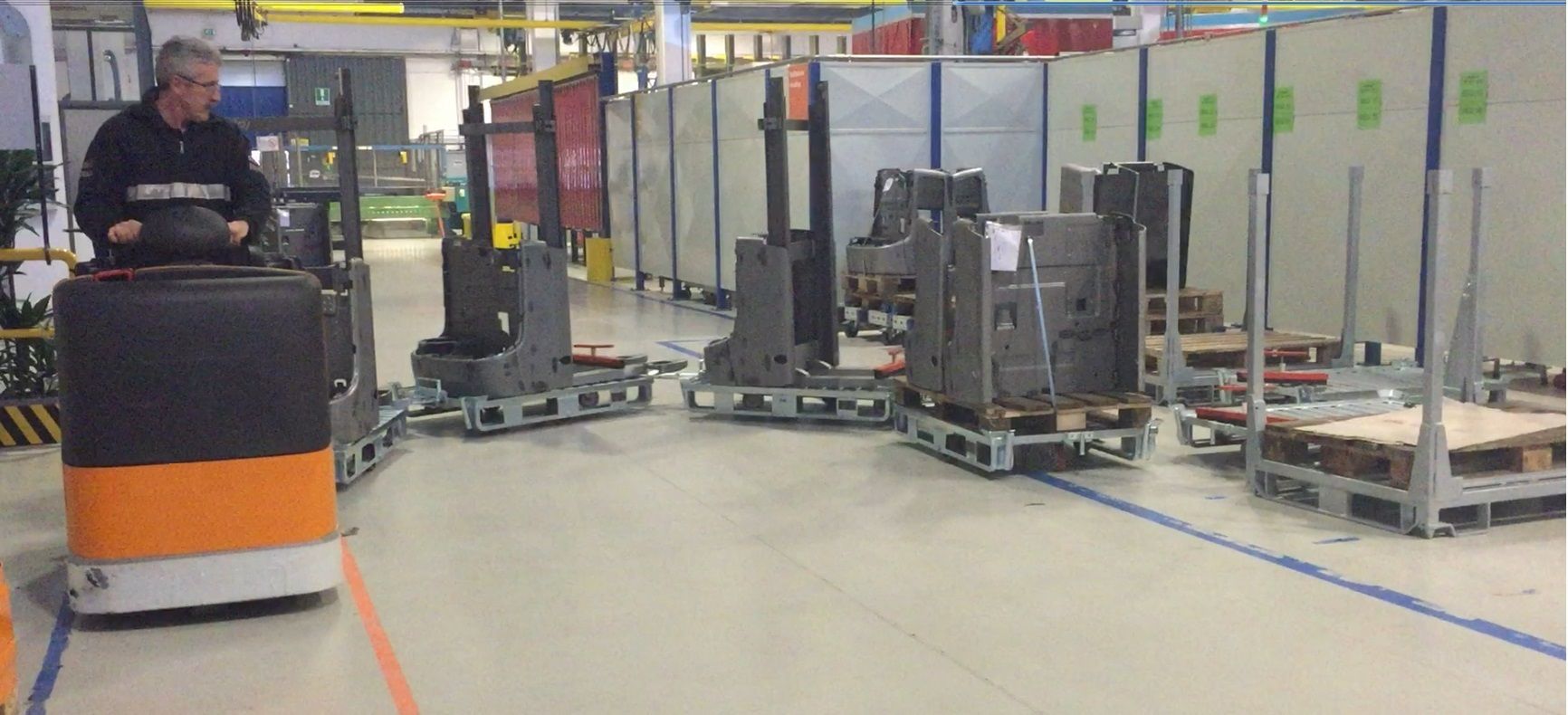
Se è possibile organizza il carico dei carrelli in modo da tenere raggruppati i materiali per destinazione.
Se carichi i carrelli manualmente fai attenzione al ergonomia nello studio del carrello e nel dimensionamento delle UDC dal acronico “Unità Di Carico” cercando di non superare i 10kg per cassetta. Puoi dotare i carrelli di un telo di copertura in caso dovessero attraversare percorsi al esterno, per proteggere da:
- Agenti esterni.
- Polveri.
- Acqua.
- Sole.
Il magazzino centrale deve essere facilmente accessibile alla logistica di approvvigionamento Milk Run, e il materiale prontamente disponibile. Il materiale può essere gestito su scaffali a gravità “supermarket” con logica FIFO o in caso di quantità più elevate può essere stoccato a pavimento su pallet con chiara identificazione dei componenti. Se il materiale è prelevato manualmente cerca di progettare gli scaffali modulari in logica ergonomica.
Spesso il magazzino viene utilizzato per il reimballaggio. Se i componenti ti arrivano in contenitori non idonei al asservimento alle linee, per dimensioni o tipologia di materiale (tipo cartone) diventa fondamentale suddividerlo in cassette in plastica riutilizzabili più piccole denominate VDA KLT studiate per ottimizzare gli ingombri e proteggere il materiale utilizzandoli anche in ambienti protetti (clean room) che poi saranno gestiti dal Milk Run.
L’utilizzo di contenitori ritornabili favorisce la standardizzazione di lotti consegnati consentendo una migliore controllo dei flussi produttivi, favorendo l’implementazione di sistemi di gestione di produzione tipo PULL.
Questo anche mediante l’uso del sistema Kanban (etichetta contenente l'indicazione materiale e la quantità richiesta) e la loro consegna ai fornitori per successivi rifornimenti. I vantaggi sono: quantità minori da gestire quindi fornitura più snella e sostituzione del cartone o di altri rifiuti dalla linea con cassette facili da utilizzare.
Un'alternativa è il Kitting, dove l'operatore seleziona le parti diverse in un kit. Il vantaggio del kit è la massima flessibilità nel fornire parti personalizzate così come richiesto dal montaggio azzerando completamente le scorte.
La grande sfida è assicurarsi zero errori di prelievo. Eventuali disguidi, possono comportarti la mancata sequenza delle parti o il fermo linea o costose rilavorazioni. Per questo un sistema Poka Yoke “Pick to Light” può esserti d’aiuto, identificando il kit occorrente ti indica in sequenza i componenti da prelevare e in quale quantità.
A destinazione, in postazione di montaggio è necessario un SAG o Supermarket completo di corsie scorrevoli o scivoli per la gestione FIFO delle parti. L’addetto all’asservimento linea caricherà dal retro i contenitori pieni e rimuoverà le cassette dalle corsie di ritorno vuote. Ogni corsia è assegnata a un unico componente.
La sfida più grande quando si imposta un sistema Milk Run nella logistica aziendale è la pianificazione, la creazione del percorso e il timing. Questo è il fattore determinante di fattibilità, e può richiedere molte prove.
Il layout della fabbrica è fondamentale per impostare i percorsi del Milk Run. Le aree del percorso e la distanza dalmagazzino alle diverse stazioni di assemblaggio svolgono un ruolo importante nel efficienza del percorso.
L’ausilio di tecniche di gestione Kanban, nella sua applicazione più moderna E-Kanban, consente all’addetto in produzione di effettuare il riordino del materiale al fornitore non appena viene consumato, semplicemente leggendo il barcode del cartellino presente sulla cassetta KLT in cui è contenuto o con l'applicazione di sensori wireless sulle corsie dello scaffale che si attivano con la rimozione della cassetta e inviano un segnale al sistema di controlle centrale di approvvigionamento, garantendosi la giusta disponibilità di scorta a bordo linea.
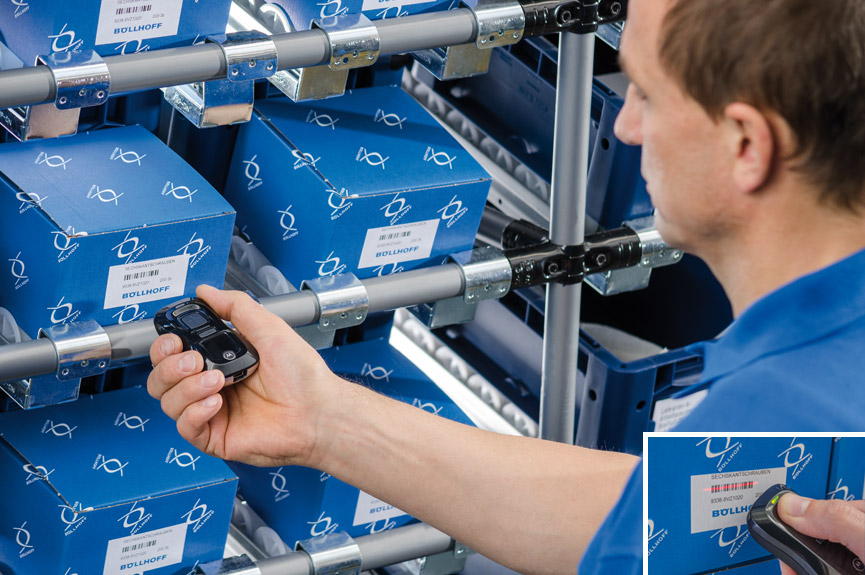
Calcoli per il dimensionamento del Milk Run
Dopo tutta la teoria sul sistema Milk Run, finalmente passiamo ai calcoli per i dettagli quantitativi. Per dimensionare correttamente un sistema Milk Run bisogna aver ben chiaro alcuni fattori logistici:
- Spazio sulla postazione di lavoro
- Frequenza di passaggio
- Materiale neccessario
- Capacità del treno
- Layout
Un analisi costi benefici ti guiderà verso la soluzione ottimale. Il fattore più critico è lo spazio in linea di montaggio, quindi l’obbiettivo del Milk Run è ridurne al minimo l’utilizzo. Iniziamo a capire di quanto materiale abbiamo bisogno sulla linea. Dobbiamo sempre avere almeno una scatola per tutto il tempo.
Quando svuotiamo un contenitore, il Milk Run lo raccoglie al primo giro e al successivo riporta il pieno. Nel caso peggiore il contenitore si svuota appena dopo il passaggio del Milk Run. Quindi, cosa succede?
In questo caso devi aspettare un ulteriore ciclo per l'approvvigionamento. Pertanto abbiamo bisogno di spazio sufficiente in postazione per due cicli del Milk Run più una scatola! Questa scatola extra è il buffer di sicurezza per le fluttuazioni del tasso di consumo in montaggio. Durante il normale funzionamento metà dei materiali (più il buffer di sicurezza) si trovano in postazione di montaggio, il resto si trova sul Milk Run e in magazzino.
Come stimare il tempo ciclo del Milk Run?
Quale è la frequenza di passaggio del Milk Run? Uno ogni due ore, ogni ora, mezz’ora, quindici minuti? Più breve è il tempo ciclo, meno materiale serve in stazione di montaggio, viceversa più è alto maggiore sarà la quantità di materiale necessario. In tutti casi imposta il tempo ciclo in modo regolare.
Usa intervalli di un ora o divisioni uniformi dell’ora (trenta minuti o quindici minuti), il conducente e gli operatori avranno modo di monitorare il sistema senza doversi chiedere quando arriverà il prossimo asservimento.
Quanto materiale per coprire due tempi ciclo? Devi determinare i materiali che ti servono al montaggio, il tasso di consumo e le unità di carico. Supponiamo di aver bisogno di un pezzo ogni 60 secondi Consumption Takt. Se l’Unità Di Carico UDC è 10 pezzi, un contenitore sarà sufficiente per 10 minuti. Quindi se il tuo tempo ciclo “Cycle Time” è 1 ora avrai bisogno di 6 contenitori + 1 (7 contenitori per questo componente).
N° Cassette = (2 * Cycle Time) / (Consumption Takt * UDC) + 1
Questo calcolo deve esser ripetuto per tutti i materiali da approvvigionare con il Milk Run. Il tasso di consumo e le unità di carico possono variare a seconda del materiale.
Come dimensionare il Milk Run?
Dopo aver calcolato le scorte necessarie per impostare un sistema Milk Run dobbiamo dimensionare correttamente lo spazio necessario sul treno. Per ogni componente dobbiamo ritirare le scatole vuote solo dopo la consegna delle piene. Quindi, come dimensionare il Milk Run? semplice, un ciclo di contenitori per tutti i componenti, oltre ai buffer di sicurezza. Ai calcoli precedenti, il numero totale di scatole per dimensionare il treno:
N° Cassette = Cycle Time / (Consumption Takt * UDC)
Come pianificare il layout del Milk Run?
Pianifca le stazioni. Crea un elenco di fermate in cui il Milk Run dovrebbe fornire il materiale indicando quali materiali servire. Poi devi determinare il percorso, questo viene fatto collegando le fermate in modo logico.
Tieni in considerazione il tempo necessario per eseguire il percorso (deve essere inferiore al tempo ciclo usato nei calcoli), considera un buffer di sicurezza nella pianificazione. Se la corsa rimane indietro, l’intera linea di montaggio si rallenta. Un'alternativa al guidatore umano sono i veicoli a guida automatica AGV.
Ci sono alcuni fattori da considerare nel calcolo dei tempi:
- Tempo necessario per percorrere il percorso.
- Di fermata con relativi carichi e scarico materiali.
- Tempo necessario per caricare il treno Milk Run in magazzino.
Le scatole vuote devono essere riempite? Questa operazione può comportare tempi maggiori rispetto la consegna alla stazione di montaggio, soprattutto se richiedono ulteriori lavorazioni di rimballo o taglio.
La maggior parte dei treni Milk Run sono composti da cinque vagoni, ma questo dipende dal tuo layout, deve essere in grado di muoversi in sicurezza e facilmente lungo il percorso.
Quindi riassumendo, per iniziare la pianificazione del percorso dal magazzino aggiungi le fermate compresi i tempi correlati (tempo di guida, di fermata e di carico). Unisci le fermate in senso logico lungo la linea. Ogni volta che raggiungi il tempo limite o lo spazio disponibile sul treno, chiudi il ciclo e inizio il successivo.
Non dimenticare di considerare il viaggio di ritorno. Quando si crea un sistema Milk Run è fondamentale monitorarlo per giorni o settimane, consultando i conducenti e gli addetti al montaggio per eventuali problemi. Potresti dover aumentare le soste o la frequenza di consegna, utilizzare scatole più piccole ecc...
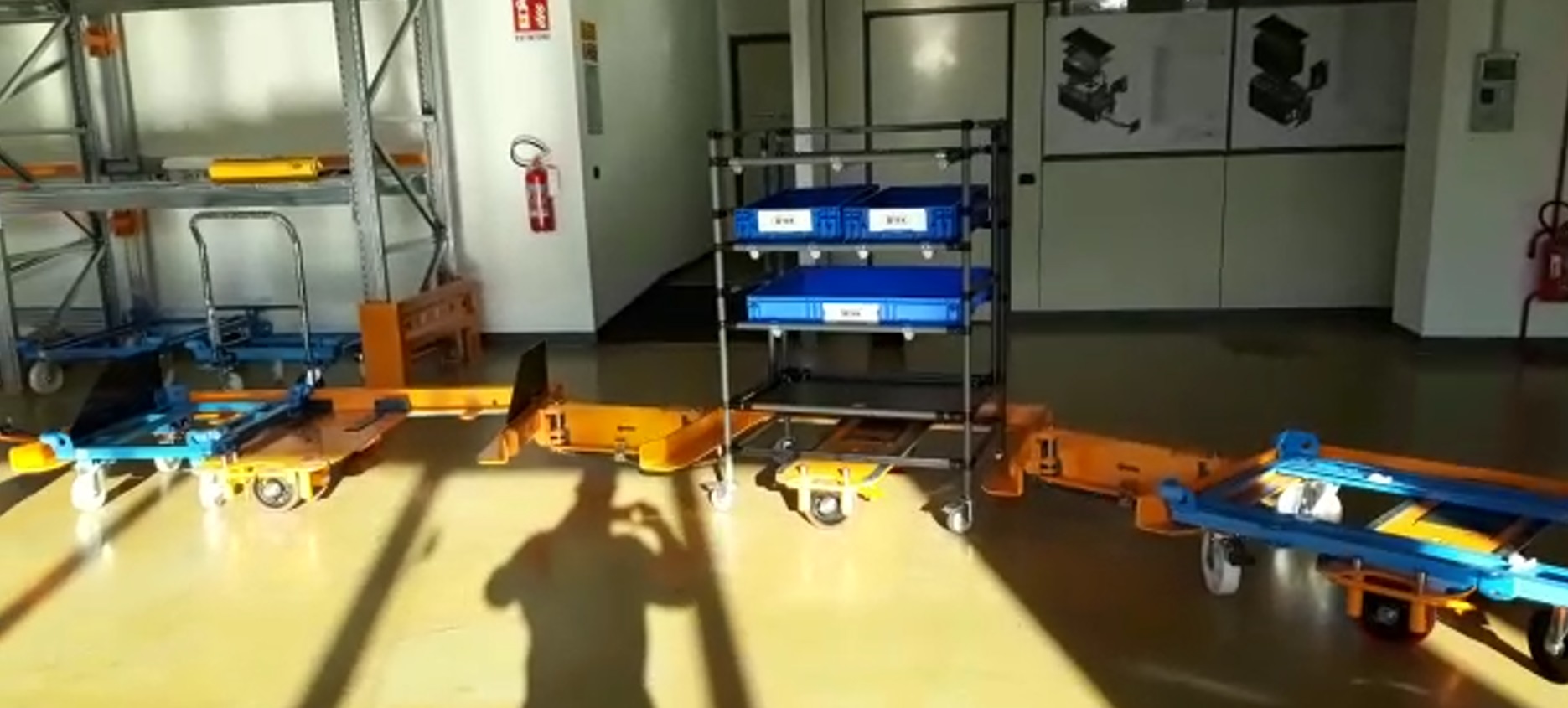
Portare la logistica Milk Run nella tua azienda
C'è la possibilità d'implementare un sistema Milk Run? Fa parte di un implementazione più ampia del processo snello per renderlo veramente efficace. Non è sufficiente solo un treno logistico per implementarlo correttamente, ci vogliono anni di pratica prima di raggiungere un risultato efficiente.
Utek grazie alla sua esperienza nel organizzazione dei magazzini e nella intralogistica si propone come partner di riferimento per implementare sistemi Milk Run per snellire e razionalizzare la propria logistica. Inoltre il concetto di Utek consente ai nostri clienti di creare carrelli di movimentazione materiali in grado di trasportare qualsiasi tipo di componente che si desidera rifornire nelle varie linee di produzione in ergonomia:
- Carrelli AGV
- Trattori Elettrici
- Sistemi di trasporto
- Sistema Dollies
- Roll-Pallet
- Trolley porta pallet
- KLT-Lifter
Questi prodotti sono fondamentali per organizzare la logistica nella tua azienda. Con la gamma Intralogistik ottimizzi il Material Flow e la fornitura alla linea, hai la possibilità di fornire materiali all'interno e all'esterno dell'azienda, riducendo così i costi logistici, nonché i tempi di produzione e di consegna.
Intralogistik di Utek include il sollevatore KLT-Lifter, che solleva automaticamente le cassette all'altezza di lavoro desiderata, i carrelli porta contenitori Dolly in diverse dimensioni progettati per utilizzo individuale o in treni logistici Milk-Run o Tugger Train.
Evidenziamo il Dolly Pallet come elemento per l’intralogistica e il flusso di materiale. È uno dei prodotti LEAN più innovativi che consentono di collegare la logistica interna all’esterna, essendo in grado di caricare Dolly 600 × 400 o 600 × 800 in modo sicuro e consentire il loro trasporto senza la necessità di ulteriori manipolazioni manuali.
Possiamo affermare che, con l'integrazione negli impianti di produzione di: Trattori Elettrici o AGV, carrelli dollies, sistema di trasporto Milk Run o treni logistici, Dolly Pallet, FiFo Monorail, e sistemi di sollevamento Lifter KLT, il controllo della gestione operativa è ottimizzato all'interno di una catena di approvvigionamento, aumentandone la produttività e la standardizzazione, riducendo le scorte ed evitando inutili manipolazioni del prodotto.
Per fare questo hai bisogno di una pianificazione ben strutturata, basata su uno studio attento di ogni dettaglio dall'organizzazione degli scaffali.
Stai cercando d'iniziare con una logica Milk Run?
Contattaci info@utekvision.com saremo in grado di proporvi la soluzione più adatta alle vostre esigenze!