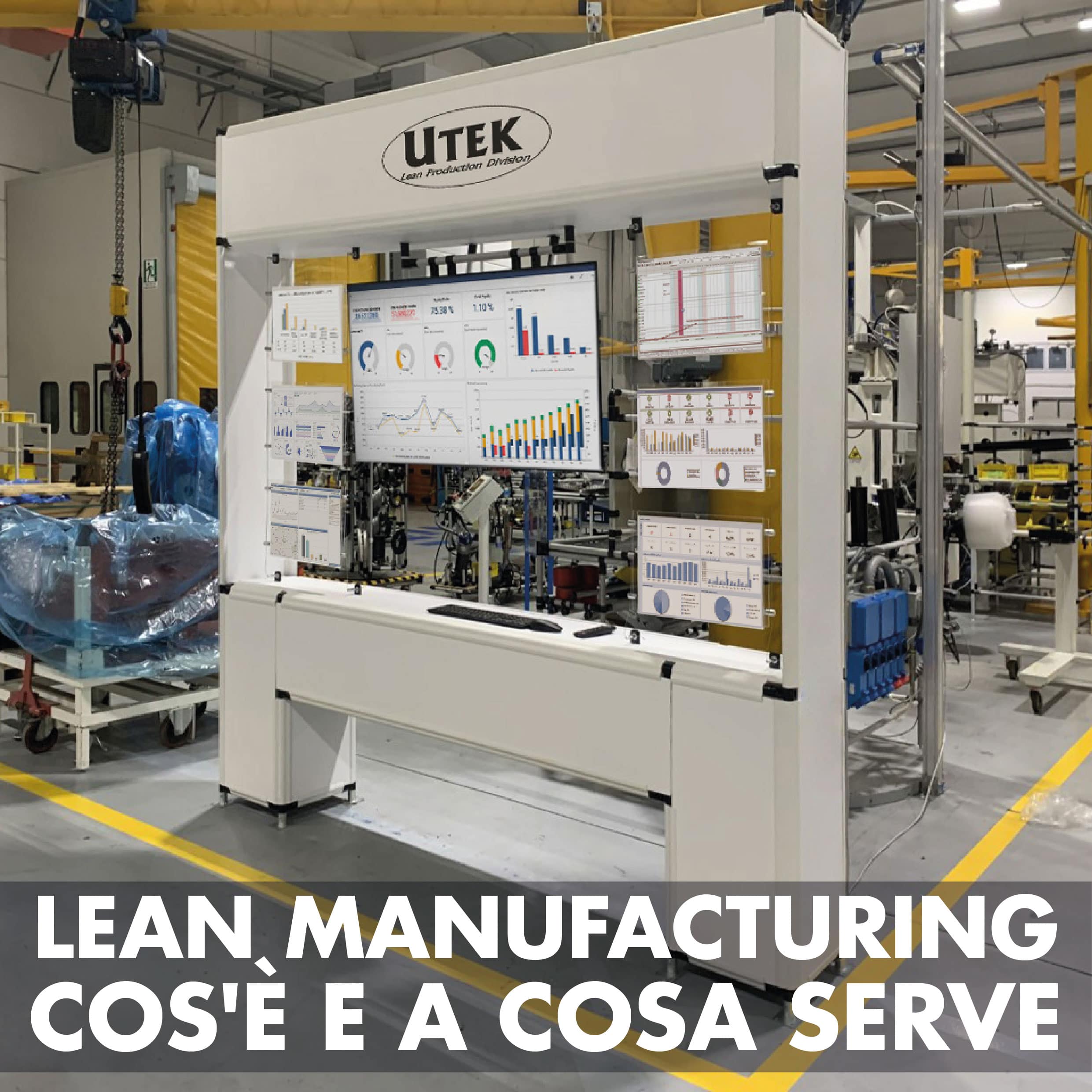
Quando si parla di Lean manufacturing si intende un insieme di pratiche e strumenti atti a implementare l’efficienza produttiva di un’azienda, per poter creare prodotti o servizi, massimizzando le risorse necessarie. Tutto ciò che non porta valore al cliente è spreco e pertanto va evitato o eliminato. Il successo della produzione snella inizia intorno agli anni ‘90 grazie alla definizione che ne danno Womack e Jones nella pubblicazione “The Machine that change the world” e cresce negli anni fino sviluppandosi anche in Europa.
Poi la Lean Manufacturing si è evoluta nel tempo e rappresenta un punto di riferimento per le aziende che vogliono migliorare ogni singolo aspetto della produzione. Numerosi studi oggi dimostrano infatti come l’insieme delle pratiche di Lean Manufacturing (OELM – Operational Excellence e Lean Manufacturing) rendano le aziende più produttive. Ma di cosa stiamo parlando?
Cos'è la Lean Manufacturing? Ecco quello che devi sapere per avere un approccio nei confronti di questa materia così importante per portare un'azienda al suo stato di eccellenza e ottimizzazione.
Lean Manufacturing, definizione
Con Lean Manufacturing intendiamo la produzione snella, questa è la traduzione letterale e ufficiale.
Ma, nello specifico, ci riferiamo a quelle tecniche e strategie che consentono di ottimizzare l'attività produttiva di un bene in azienda. L'obiettivo finale è la possibilità di aumentare il profitto
Ciò avviene ottimizzando le risorse, riducendo gli sprechi e migliorando l'efficienza delle attività produttive e logistiche. Questo si basa su 5 principi che sono definiti le 5S della Lean Manufacturing:
- Seiri – Scegliere e separare, togliere il superfluo.
- Seiton – Sistemare e organizzare ciò che serve.
- Seison – Verificare la pulizia della postazione di lavoro.
- Seiketsu – Standardizzare e migliorare ogni punto.
- Shitsuke – Mantenere nel tempo il rigore operativo.
Ovviamente per mettere in pratica queste attività non basta solo avere un obiettivo condiviso, hai bisogno anche di competenza per studiare la migliore strategia e strumentazione adeguata. Proprio come quella che puoi trovare nel catalogo di Utek. Puoi dare uno sguardo qui.
Lean e Six Sigma
Lean e Six Sigma sono due metodologie che spesso vengono confuse perché hanno obiettivi molto simili e si focalizzano entrambe sull’eliminazione degli sprechi, la sostanziale differenza si concentra sulle tecniche utilizzate per raggiungere tali scopi.
Lean concentra il proprio lavoro sulla creazione di flusso durante tutto il processo produttivo, assicurandosi di ridurre al minimo ogni forma di spreco, avvicinando le parti e favorendo pratiche just in time per eliminare tempi di fermo dovuti ad attese o riordini. JIT non snellisce solamente il flusso ma limita anche l’accumulo incontrollato di scorte in eccesso che comporta costi di stoccaggio e mantenimento.
Six Sigma dalla sua si concentra invece sui difetti che non devono solamente essere eliminati, per far scorrere il flusso di lavoro ma desidera comprendere e analizzare a fondo le cause per poi evitare che si ripropongono.
Due tecniche accomunate dall'obiettivo finale e che se utilizzate in sinergia, approccio conosciuto come Lean Six Sigma, possono fare la differenza su una produzione di qualità e dal valore aggiunto.
Quali sono i benefici della Lean Manufacturing?
In questi casi devi dare risalto a quelli che sono i punti a favore della Lean Manufacturing. O meglio, di questo circuito organizzativo che ti permette di rivedere il modo d’intendere l'azienda.
Quali sono i pro della Lean Manufacturing? In primo luogo c'è un aumento dell'efficienza produttiva. Poi si riporta all'attenzione la diminuzione dei costi, degli imprevisti e degli infortuni. Proprio è nella logica della produzione snella aumentare la sicurezza: Aiuta a evitare inutili perdite di tempo.
La Lean Manufacturing comporta riduzione di attività inutili e dei materiali in eccesso, movimenti superflui, produzioni inutili al fatturato e tempi di attesa che potrebbero essere utilizzati diversamente.
Questi obiettivi non sono troppo lontani e neppure di difficile raggiungimento ma la cattiva organizzazione dei processi produttivi può minarne il lavoro.
Per cattiva organizzazione sono da intendersi ad esempio: Tempi di produzione eccessivi, mancanza di un controllo tramite adeguati KPI, controlli carenti, attrezzature e ambienti di lavoro non scelti adeguatamente e mal gestiti, mancanze nella progettazione delle attività da svolgere e formazione carente.
Principi alla base dell’implementazione snella
Chiarito il perché è vantaggioso implementare tecniche di Lean Manufacturing nella propria azienda, è giusto riassumere anche 5 principi alla base della sua implementazione.
Questi 5 punti nascono da una pubblicazione del 1996 intitolata “Lean Thinking: Banish Waste and Create Wealth in Your Corporation” e dalla quale sono stati estrapolati una serie di concetti fondamentali: Valore, Flusso di valore, Flusso, Attrazione e Perfezione.
- Definire cos’è il “valore” per il cliente perché bisogna ricordarsi sempre che questa “caratteristica” viene ricercata da tutti ma è il produttore colui che la genera e il cliente ne definisce la “forma”, decidendo poi se abbastanza soddisfacente da essere disposto a pagare per essa. Eliminare gli sprechi permette all’azienda di definire un valore che il cliente è disposto a pagare e che allo stesso tempo massimizza il profitto.
- Mappare il flusso di valore è fondamentale per identificare dove si nascondono sprechi e aspetti da migliorare. Non sempre si tratta di tagliare o eliminare, parte del lavoro consiste anche nel allineare gli elementi del flusso affinché lavorino in sinergia per raggiungere l'obiettivo finale.
- Oltre a capire quali attività sono a valore o meno nel processo produttivo, è necessario anche focalizzarsi sulla creazione di flusso e per farlo bisogna prestare attenzione ad aspetti come i tempi di lavoro dei singoli step, la prevenzione d’interruzioni al processo produttivo e sul lavoro di stretta collaborazione tra le varie fasi produttive.
- Oltre a un flusso continuo e incentrato sulla creazione di valore, è giusto organizzare il processo affinché la produzione venga spinta (attratta) dalla domanda e non dall’idea di creare scorte e inventario per sopperire alle nuove richieste. Stabilire un sistema Pull comporta però un buon livello di organizzazione, flessibilità e comunicazione.
- Individuare gli sprechi causa di perdita di valore non è la conseguenza di una mappatura del flusso di lavoro ma un’attività da perseguire ogni giorno per la continua ricerca di miglioramento, anche detto Kaizen.
Quali sono i tre rami della produzione snella?
Ecco i tre grandi settori della Lean Production, riguardano tutti la gestione. Che può essere della progettazione, produzione e qualità. Alla base di questo passaggio tra diversi tipi di flussi abbiamo la movimentazione che deve essere veloce, senza ostacoli e difficoltà.
Tutto questo è necessario per eliminare i problemi tipici di un'azienda - anche di piccole dimensioni - che procede a caso: ridurre per poi eliminare la produzione extra e inutile, diminuire i ritardi, non dare forza alle attività inutili, ridondanti e poco utili al fine della produttività.
Strumenti di produzione snella
Una struttura che si basa sulle tecniche di Lean Production utilizza in realtà un’ampia gamma di tecniche e metodologie atte a implementare le prestazioni aziendali e ridurre gli sprechi. Lean trae vantaggio da un’ampia gamma di strumenti, scelti strategicamente per asservire al meglio ogni situazione.
Tra gli strumenti Lean più famosi e di più ampio utilizzo troviamo:
- 5S ovvero cinque fasi che servono per individuare varie forme di rifiuto, ognuna con iniziale S (Seiri – separare, Seiton – riordinare, Seiso – pulire, Seiketsu – standardizzare, Shitsuke – sostenere)
- Jidoka è un concetto che combina automazione e intervento umano, concretizzando nel blocco immediato di un macchinario / lavorazione non appena viene individuato un problema, in modo da comprenderne subito le cause e risolverlo tempestivamente. Questa tecnica può causare blocchi momentanei ma a lungo andare consente di avere un work flow fluido e con meno intoppi.
- Kanban è una tecnica di gestione del flusso delle parti lungo la catena produttiva che sfrutta dei cartellini associati a ogni pezzo che entra nel flusso, per sapere in ogni momento dove si trova e quando è necessario riordinare parti o farle entrare in produzione. Questa pratica assicura maggiore efficienza produttiva e riduzione di casi di sovrapproduzione.
Cosa fà il Lean Manager nella produzione?
Il Lean Manager è la persona che si occupa della gestione dell'attività di ottimizzazione dei vari passaggi. Anche la produzione snella è in mano al Lean Manager che in questo frangente si occupa di tutto ciò che riguarda i meccanismi di ottimizzazione della catena virtuosa.