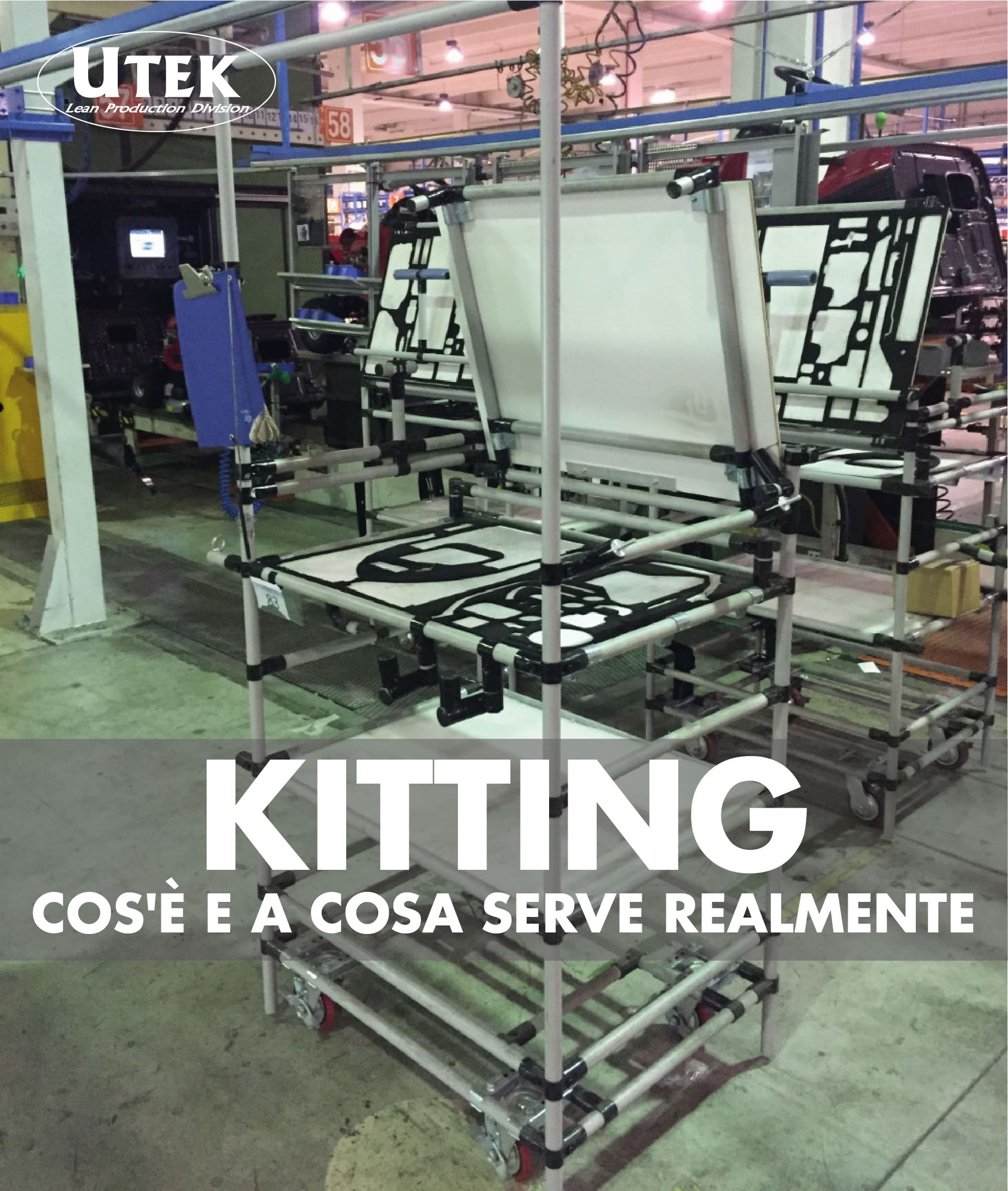
Il kitting nella logistica è un processo che consiste nell'assemblare insieme un insieme di elementi correlati, solitamente parti di un prodotto, in un unico kit o set predefinito, in modo che possano essere utilizzati facilmente per completare un'attività o un'operazione specifica. Il kitting può essere utilizzato in diverse fasi della logistica.
Indice dei contenuti
Oggi dobbiamo scoprire e approfondire il Kitting. Si tratta di una metodologia per ottimizzare le operazioni che si svolgono nella linea di assemblaggio nelle aziende manifatturiere (ma non solo). Vuoi sintetizzare il tutto?
Il Kitting deriva da Kit, e si tratta di una soluzione che permette di raccogliere tutti gli elementi utili all'assemblaggio di un prodotto lasciandoli in punti stabiliti - e sempre uguali - che corrispondono appunto a kit di montaggio.
Questa metodologia ha il pregio di ridurre i tempi necessari al montaggio di componenti complessi, con un gran numero di elementi, perché riduce il tempo di movimentazione delle parti. Chi deve montare sa già dove trovare quello che serve per creare il prodotto. E non deve spostarsi, chiedere pezzi e muovere mezzi di locomozione.
Cos'è il Kitting, il significato
Con il termine Kitting (dall'inglese kit, insieme di elementi) intendiamo una metodologia utilizzata nei processi di lean production per ridurre i tempi di montaggio di un prodotto. Questa strategia di gestione delle scorte è utilizzata per ottenere pacchetti di componenti pre suddivisi ed etichettati, aumentando così l’efficienza del flusso di lavoro e riducendo tempi e costi legati all’organizzazione di alcune tipologie di prodotto particolarmente impegnative.
L'obiettivo è ridurre i tempi necessari al montaggio degli oggetti più complessi e articolati. Quindi si risparmia su una risorsa ben nota: il tempo. In questo modo è possibile ridurre gli sprechi e rispettare il principio della lean organization che spinge a eliminare tutto ciò che è muda, ovvero spreco, per raggiungere la perfezione.
Ogni elemento viene migliorato, analizzando il ciclo di Deming per fare in modo che ogni passaggio sia migliore. Meno impegnativo. Il metodo Kitting, ovvero creare dei kit di montaggio organizzati, lavora in questa direzione.
Quali sono le fasi del Kitting?
Si decide il kit da preparare in base alle esigenze tecniche. Poi si valutano scorte e acquisti per rimpinguare il magazzino e adeguarlo alle esigenze, si individua un metodo per emettere il kit e si permette a un addetto di caricare il carrello con gli elementi organizzati in modo da semplificare l'accesso dei vari pezzi agli operatori.
Questo processo si basa su una metodologia just in time, in cui ciò che serve viene ordinato e aggiunto ai vari scaffali. Chiaramente la scelta dei fornitori è fondamentale per consentire un approvvigionamento puntuale e preciso: se ritardano i pezzi necessari al processo cade l'intera utilità del kitting nella logistica aziendale.
A cosa serve il metodo Kitting
L'obiettivo è ridurre il lead time nel montaggio. Ciò avviene mettendo insieme pezzi del montaggio che in origine sono separati, situati in zone diverse del magazzino. Questo metodo consente a un'unità di produzione di sapere sempre dove si trova ciò che serve, rispettando un altro punto chiave della lean organization: standardizzazione.
Non devo perdere tempo in movimentazione superflua e spostamenti inutili. Ma non devo neanche contare sulla presenza di un kit di montaggio che oggi c'è, domani no e dopodomani non ha tutti i pezzi necessari per l'assemblaggio: il successo del Kitting si basa sulla condivisione del metodo 5S e sulla sua costanza nel tempo.
Come organizzare i magazzi ai kit
Il metodo kitting è possibile solo se il magazzino è in grado di garantire certe caratteristiche: facilità di accesso alle scorte, possibilità di stoccare le tipologie di prodotto, indipendentemente da dimensione e composizione, organizzare la merce in magazzino per rendere più efficiente il prelievo e le movimentazioni.
Questi aspetti indispensabili per l’implementazione di una strategia di kitting possono essere resi possibili grazie ad attrezzature e una organizzazione del magazzino in ottica lean production e organizzazione snella.
Stiamo parlando di scaffali a gravità per il picking dotati di rulliere in grado di facilitare il prelievo in ottica FiFo e carrelli kitting. Tutto questo è fondamentale per migliorare la tua strategia di kititng nella logistica aziendale.
Vantaggi e svantaggi del Kitting
L'applicazione di questa metodologia destinata alla logistica - senza le giuste risorse e il tempo necessario - rischia di non dare i benefici sperati. Quali sono i vantaggi ai quali puntare per ottenere valore aggiunto?
Riduzione work-flow e coordinazione delle aree di lavoro
Tramite la preparazione di kit il materiale impiega minor tempo ad arrivare alla linea di produzione e l’operatore addetto alla lavorazione non deve perde tempo nella ricerca dei componenti perché già a portata di mano.
Riduzione muda ed errori
Se il kit viene preparato e consegnato all’operatore si riduce il rischio di errori dovuti all’utilizzo di componentistica sbagliata e di sprechi da lavorazioni non necessarie. Allo stesso modo è possibile dimenticare di assemblare un componente rischiando di produrre un prodotto fallato. In questo ci vengono incontro dispositivi pick to light collegati a un sistema gestionale automatizzato del magazzino per maggiore precisione di prelievo e controllo.
Gestione visiva
Nelle linee di produzione spesso si alternano più turni di operatori che vanno ad adoperare le medesime postazioni, proseguendo le attività iniziate il turno precedente. Questo comporta però il rischio di errori dovuti alla non comunicazione tra i vari operatori, facendo un esempio, un kit assicura che tutti i componenti di un pezzo vengano riconosciuti visivamente e utilizzati, anche se vi fosse un cambio di personale.
Maggiore efficienza produttiva
La preparazione di kit snellisce i tempi di lavoro e crea un flusso quasi ininterrotto della produzione. Il continuo prelievo di materiale dal magazzino per l’attività di kitting favorisce anche un controllo costante delle scorte evitando così potenziali blocchi produttivi causati dalla mancanza di materie prime.
Ottimizzazione degli spazi
Questa tecnica prevede il trasporto sulla linea produttiva dei soli componenti necessari al lavoro su di un carrello kit, ottimizzando lo spazio a disposizione per le attività lavorative. Questo è uno dei vantaggi del kitting.
Riduzione imballi superflui
Se determinati prodotti vengono forniti dal distributore direttamente in kit, questi vengono stoccati in minor spazio e con un unico imballo. Meno imballi utilizzati implicano anche meno rifiuti prodotti da smaltire.
Riduzione rischio danneggiamenti
Le singole parti da quando vengono prelevate a magazzino a quando giungono alla postazione rischiano di essere danneggiate, cosa che non avviene se un unico kit imballato viene portato alla linea di produzione.
Quali sono i problemi del metodo kitting?
- Non standardizzazione del processo.
- Fornitura imprecisa per colpa degli utenti.
- Fornitura imprecisa per mancanza di materia prima.
- Non comunicazione delle carenze.
La creazione di kit è un metodo sicuro per prevedere errori a livello produttivo ma non impedisce la perdita di componenti tra il loro arrivo in postazione e l’utilizzo effettivo. In queste circostanze nasce però un problema legato alla sostituzione del pezzo in quanto il kit non prevede parti da sostituire. Il kitting è una tecnica vantaggiosa per l’efficienza produttiva ma il vantaggio termina quando i muda che comporta sono inferiori a quelli che rimuove.
Kitting, strategie per ottimizzarlo
Come ogni parte del sistema di gestione Lean della produzione, il kitting dovrebbe basarsi su un processo ben standardizzato. Pertanto quando decidi d’implementare questo meccanismo nella tua produzione assicurati di:
- Sviluppare un modus operandi base per il work in process
- Crea un metodo di lavoro standard
- Assicurati che i kit siano riconoscibili visivamente
- Basa i rifornimenti solo su segnali pull.
Ottimizzazione del magazzino e delal logistica
Il sistema kitting consente di ottenere di più da meno, e aumentare il valore creato dalla produzione, partendo da un minor numero di SKU perché ogni prodotto è gestito in assiemi composti da più elementi. Si risparmia così tempo nella gestione delle scorte, guadagnando in minori costi di produzione con maggiori entrate dal prodotto.
Questo funziona se il magazzino ha una logistica efficace e una scaffalatura per il just in time e la logica pull, in cui "tiri" ciò che serve dalla fonte (i fornitori) e non accumuli scorte. In quest’ottica è fondamentale avere:
- Carrelli AGV
- Trattori Elettrici
- Sistemi di trasporto
- Sistema Dollies
- Roll-Pallet
- Trolley porta pallet
- Inserti sagomati Shadow Board
- Cassette porta minuterie kitting
D'altro canto bisogna anche saper ottimizzare questi elementi. C'è bisogno di un piano strategico per avere la fornitura migliore ma anche una soluzione in grado di approvvigionare ciò che serve nei tempi giusti.
Per maggiori informazioni puoi contattarci a info@utekvision.com.