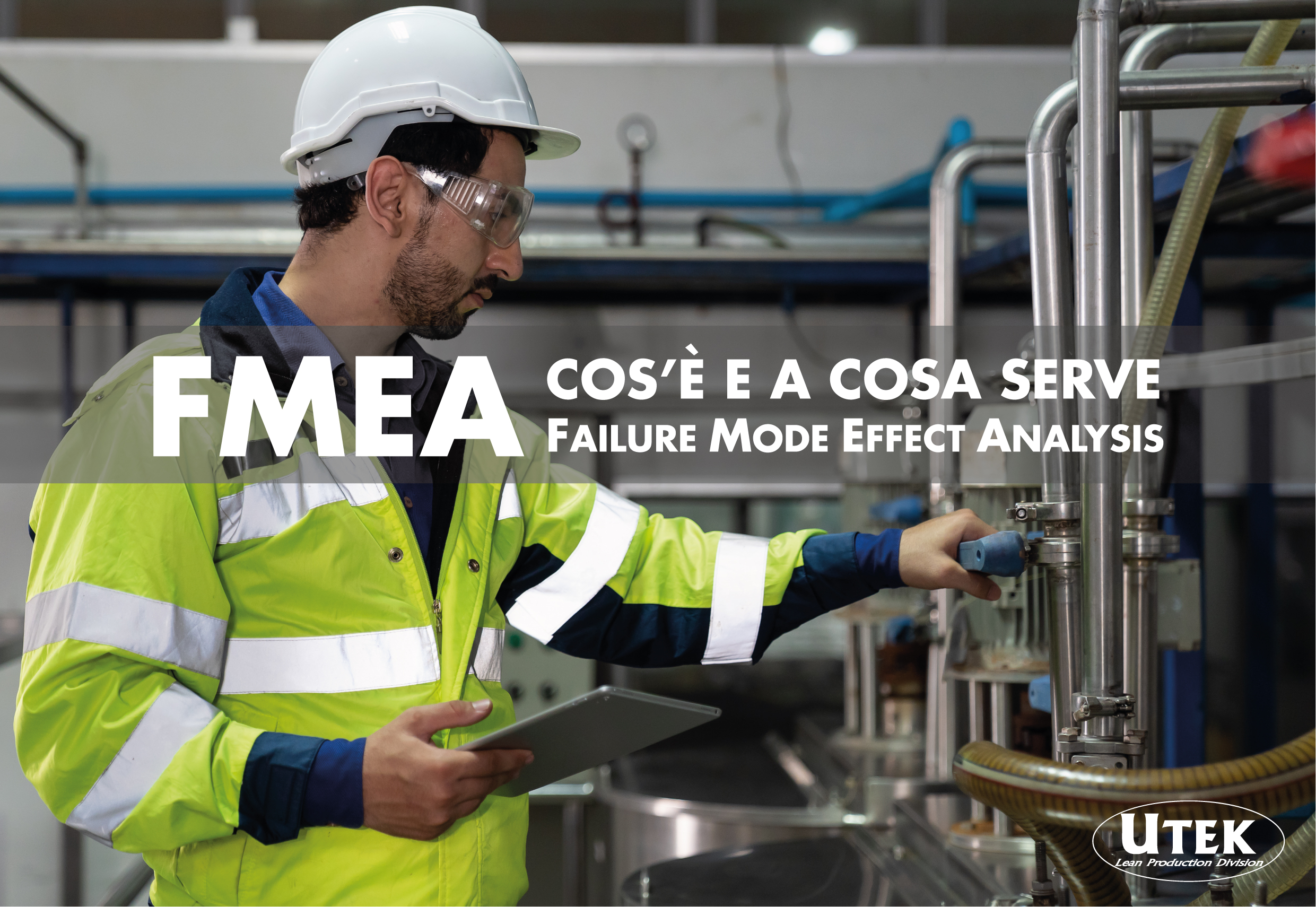
FMEA è l'acronimo di Failure Mode and Effects Analysis, analisi delle modalità di fallimento e degli effetti. È una metodologia usata per identificare, valutare e mitigare problemi o guasti che possono verificarsi in prodotti o processi industriali. Obiettivo: migliorare la gestione dei rischi e gli effetti associati a una modalità di fallimento.
Indice dei contenuti
Chi conosce la lean production, la produzione snella, ha incrociato FMEA - Failure Mode and Effect Analysis. Questa soluzione strategica serve a ottimizzare i tempi e le procedure in relazione ai guasti.
Infatti, il contrattempo è una delle piaghe che ogni azienda deve e vuole eliminare dal proprio ciclo di lavorazione. Ogni passaggio che viene bloccato da un guasto provoca un rallentamento, una perdita di tempo. Nella metodologia della lean organization possiamo parlare di muda. Vale a dire scarto, qualcosa che non serve.
Organizzazione snella significa eliminare quello che non serve per focalizzarsi sul valore. Il FMEA punta proprio a questo: dobbiamo eliminare il problema, l'eventuale causa di guasto ed errore per evitare perdite di tempo.
Analisi FMEA: cos'è, definizione
FMEA, acronimo di Failure Mode and Effect Analysis, vale a dire analisi dei modi e degli effetti dei guasti. In effetti questa è la sua definizione perché si tratta di un metodo preventivo per studiare dove si verifica un guasto o difetto di un prodotto o processo, quali sono le conseguenze cause ed effetti sul sistema e dove si deve intervenire per ottimizzare il processo. La sua caratteristica fondamentale: si tratta di un'analisi preliminare.
Quini la tecnica FMEA è utile per studiare un flusso di lavoro in modo da creare una base già efficace. Per poi lavorarci e ottimizzarla in base all'applicazione empirica. È una pratica utilizzabile a tutti i livelli di studio e progettazione di un nuovo prodotto o processo, per i piani d’implementazione e il miglioramento di attività esistenti.
FMEA di prodotto e di processo
Questi due diversi campi applicativi vanno proprio a differenziare le due tipologie di FMEA: FMEA di progetto (DFMEA) utilizzata a monte per testare nuovi prodotti o soluzioni e l’FMEA di processo (PFMEA) che studia processi e procedure già in uso e che a suo favore ha la possibilità di consultare dati di analisi parte dello storico.
Quali sono le origini del FMEA
Il termine FMEA nasce negli Stati Uniti nel 1949 come una procedura militare con l'obiettivo di conoscere tutti i possibili guasti e scoprirne in particolare gli effetti sul successo finale delle missioni, sulla sicurezza delle persone coinvolte e sugli equipaggiamenti utilizzati. Negli anni ‘60 l’idea viene estesa anche alle missioni spaziali Apollo.
Fino a raggiungere il settore automobilistico attorno agli anni ‘80 con l’azienda Ford, che ne fece uso in particolare per l’autovettura modello Pinto, la quale presentava un problema al serbatoio, causa di incidenti.
Nel 1994 tre aziende molto importanti sempre del settore dei veicoli, Chrysler, Ford e General Motors, di comune accordo, introducono l’utilizzo nelle loro produzioni del metodo FMEA. Questo metodo di analisi fa parte dei sistemi di controllo qualità e della sicurezza per molti settori, compreso quello dell’automobile.
Flow Chart, le fasi una analisi FMEA
L'analisi FMEA prevede la scomposizione degli step di un processo produttivo o distributivo per analizzare ogni causa di guasto, ogni fonte di problema che potrebbe causare stop e inconvenienti. L’FMEA si può suddividere in 5 fasi principali: preliminare, qualitativa, quantitativa, correttiva e di misurazione. L'analisi studia:
- Preparazione della metodologia scegliendo tra:
- FMEA di progetto (D-FMEA).
- FMEA di processo (P-FMEA).
- Le motivazioni che hanno portato al guasto.
- Le conseguenze che sono collegate all'inconveniente.
- Definizione degli indici di rischio I.P.R. per capire come agire.
- Studio soluzioni (introdurre sistemi poka yoke o automatismi).
- Applicazione delle decisioni prese.
- Analisi per valutare l’efficacia.
Tutto questo viene definito grazie a delle tabelle comparative che organizzano i dati per voci in modo da spiegare a chiare lettere come, quando e perché agire al fine di ritrovarsi in una situazione di partenza con zero guasti.
Quali sono gli obiettivi dell’analisi FMEA?
I vantaggi per le aziende che usano la metodologia FMEA: anticipano le fonti di guasto nel momento in cui creano il flusso di lavoro con piani di prevenzione più efficienti, migliorano le performance e l’affidabilità di processi e progetti, risparmiano tempo e costi causati dalla manutenzione e dai fermi e aumentano la sicurezza.
L'idea non è quella di disinteressarsi completamente dell'aspetto relativo al miglioramento. Attraverso altre tecniche si procede verso il miglioramento e l'abbattimento dei problemi creando una scala di priorità d’interventi e implementazioni da effettuare. Così si valuta la probabilità che una certa modalità di fallimento si verifichi.
Quali sono i valori del processo FMEA?
A ogni evento vengono definiti dei parametri I.P.R (RNP) che aiutano a valutare cosa accade in quella circostanza e come bisogna operare per ottenere risultati degni di nota (ovvero risolvere la fonte del problema):
- Occurrence: probabilità di accadimento, quando accade il danno.
- Severity: gravità del problema, quali sono gli effetti.
- Detection: rilevabilità dei controlli: l'evento si può rilevare?
A ogni voce viene dato un punteggio crescente per gravità che va da 1 a 10. Quindi, ad esempio, se diamo 1 a probabilità di accadimento (elemento sintetizzato con la lettera O) vuol dire che l'evento non accade quasi mai.
Ma se ha 10 nella voce S (ovvero gravità) vuol dire che ci troviamo di fronte a un evento sì poco probabile ma che può diventare incisivo sulla produzione. In caso di 10 alla voce D (Rilevabilità) siamo sicuri che i controlli esistenti non sono in grado di rilevare le cause o che addirittura mancano i direttamente i controlli in progettazione.
FMEA, come calcolare l'indice
Dando a ognuna delle voci elencate un parametro da 1 a 10, con un tenore di gravità del valore crescente, possiamo trovare l'indice di priorità di rischio con una semplice moltiplicazione di tutti i fattori: I.P.R = O x D x S.
Il risultato ci permette di dare una priorità agli interventi da attuare per rendere il processo produttivo, teoricamente, meno soggetto a problemi e stop. Per maggiori informazioni non esitare a contattarci info@utekvision.com! Ti aiuteremo ad avviare le misure per ridurre la probabilità o gli effetti di fallimento.