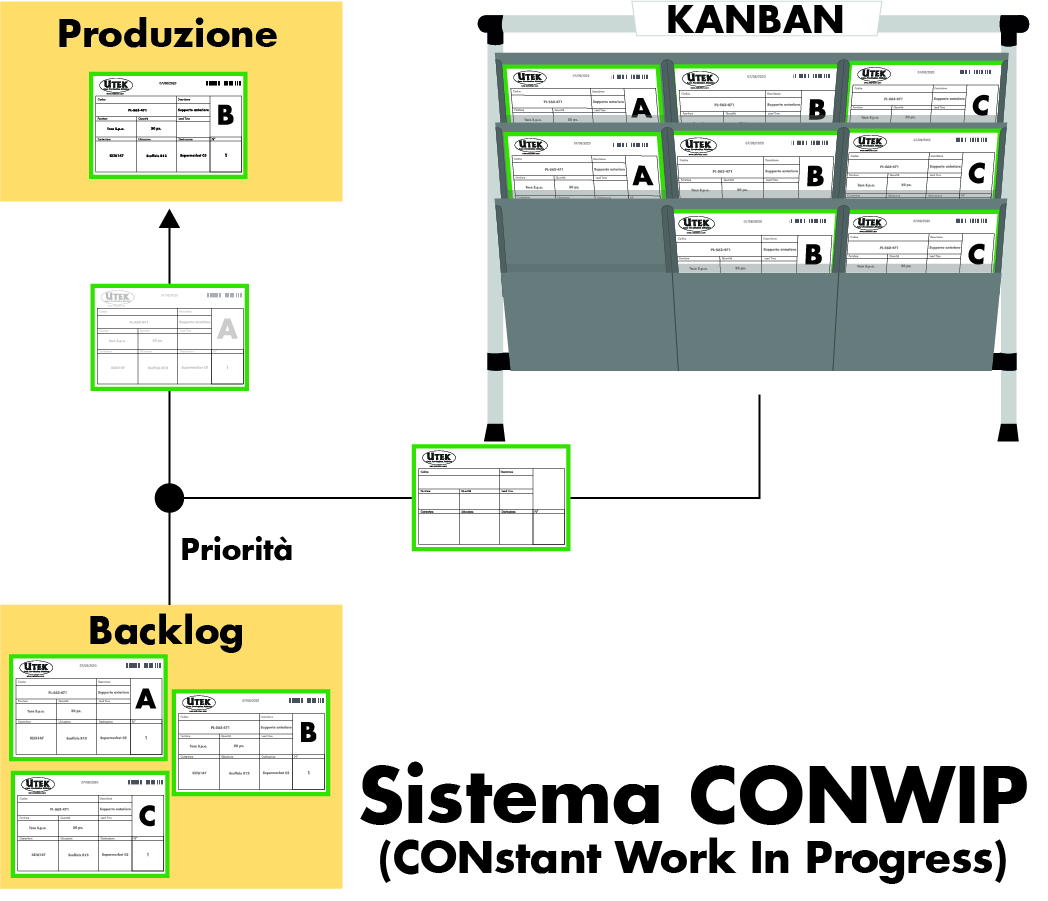
Indice dei contenuti
Il CONWIP (CONstant work in progress) è una tecnica di monitoraggio del flusso di materiale applicabile a differenti tipologie di sistemi produttivi. In particolar modo si caratterizza per la capacità di mantenere costante il flusso di elementi in movimento nel processo di lavoro, equilibrando le parti in entrata e quelle in uscita. Sviluppato da Mark Spearman e Wallace Hopp nel 1990, si basa su logica pull, può essere considerato uno strumento del kanban in quanto si regola con l'utilizzo di segnali visuali “cartellino” per autorizzare la produzione.
Pretende tre elementi fondamentali per consentire a una produzione di proseguire senza intoppi:
-
Backlog list (lista di parti da produrre)
-
Materie prime necessarie per l'operazione
-
Cartellino plastificato che regola il processo
Detto in altre parole, una produzione per accedere al flusso deve indicare le sue priorità e le informazioni sull'avanzamento del processo. Oltre a possedere già le materie necessarie per concludere la lavorazione.
In che modo avviene questo? Quali sono i rapporti tra metodologia snella e CONWIP?
Ecco cosa devi sapere per approfondire questo principio della produzione snella.
Cos'è CONWIP e cosa significa
Un sistema CONWIP, al contrario di un kanban, sfrutta un’unica tipologia di cartellini, non associata al tipo materiale ma solo alla quantità per monitorare l’intero WIP (work in progress) all’interno del flusso.
E’ una tecnica pertanto che mira a semplificare la gestione della produzione totale. Il monitoraggio non avviene più a livello della singola stazione di lavoro ma tramite un controllo generale delle quantità con il calcolo dell’ammontare dei cartellini in circolo.
Più nello specifico, all’inizio della linea produttiva a ogni lotto di materiale viene assegnato un cartellino che lo segue in tutte le lavorazioni e solo alla fine, raggiunta l’uscita, viene sganciato per essere associato a un nuovo lotto.
Pertanto se un lotto entra nel sistema di produzione vi è disponibilità di cartellini, parametro chiave che determina il massimo livello di WIP.
Il cartellino all’inizio del ciclo prima di essere immesso nel flusso di produzione, incontra il backlog, elenco di parti e quantità che sono in lista per essere prodotte.
La prima parte rimasta indietro è la priorità. Se un cartellino CONWIP associato a un prodotto terminato torna a monte, la parte successiva nella riga viene abbinata alla carta di restituzione.
I cartellini sono il segnale per la disponibilità di capacità e spetta al backlog decidere cosa farne.
Seguendo questo ragionamento, una carta CONWIP e un kanban sono uguali tranne per il fatto che la tipologia di parte viene attribuita solo al momento del ritorno quando è stata soddisfatta la richiesta più urgente del backlog.
Differenza con metodo kanban
Anche con il sistema di lavoro kanban ci muoviamo attraverso una verifica dei cartellini, o comunque di segnali che identificano un processo di avanzamento all'interno della linea di produzione.
In realtà c'è una differenza sostanziale tra kanban e il CONWIP.
Quest'ultimo spinge avanti il processo solo all’inizio della linea, mentre nel metodo kanban è spinto tra qualsiasi stazione di lavoro. Una differenza tangibile tra kanban e CONWIP consiste proprio nell’associazione dei cartellini, se nel primo caso a ogni carta corrisponde una parte, nell’altro sistema questa viene associata a una quantità costante.
Con il CONWIP si semplifica la gestione perché occorre monitorare un’unica tipologia di cartellini per controllare l’intero WIP (work in progress).
Il materiale, una volta entrato nel processo, fluisce in libertà tra le varie postazioni di lavoro come se prendesse parte a un flusso “push” e non “pull” ma c’è da tener conto di accumuli sulla linea. Il sistema kanban obbliga alla gestione di più set di cartellini associati a differenti parti ma offrono al contempo la possibilità di controllare il flusso produttivo in modo mirato, a livello della singola stazione.
Kanban gestisce bene processi con bassa varietà di prodotti e di alta quantità poiché a ogni cartellino è associato permanentemente un numero di parte.
Se invece produci soluzioni su misura o lavori su ordinazione, il kanban non è la soluzione più adatta a te.
Ti viene pertanto in soccorso il sistema CONWIP perché non avendo nessuna parte assegnata in modo costante, ogni ordine in modo temporaneo può esservi abbinato, soddisfacendo così anche le produzioni saltuarie di alcuni prodotti.
L’ultima differenza da tenere in considerazione in caso di scelta tra i due sistemi, è il contributo umano.
Se il kanban ha il punto a favore di gestire automaticamente la produzione, basta avere un numero sufficiente di cartellini per ogni parte, CONWIP invece necessita del contributo umano per dare il via al processo di lavoro.
Il backlog occupa una posizione fondamentale per il corretto funzionamento del workflow ma se si compiono errori di priorità a monte, si rischia d'incorrere nell’effetto frusta, ossia la reazione eccessiva alla richiesta di domanda.
Logica push e pull insieme
Una delle caratteristiche fondamentali della metodologia CONWIP,
è la capacità di unire due elementi chiave della logica organizzativa del flusso lavorativo.
Da un lato c'è la possibilità di sfruttare la logica pull, che è quella tipica della Lean Manufacturing: non si accumula materiale inutilmente ma si "tirano" le risorse necessarie al processo produttivo. Questo significa che si introduce un nuovo compito solo dopo il completamento del precedente.
D'altro canto non è un sistema pull puro, infatti l'avanzamento è di tipo push: finita l'operazione relativa a una stazione il prodotto viene spedito alla fase successiva.
Benefici del CONWIP
Il sistema CONWIP come detto poco prima è un metodo funzionale per il controllo dei quantitativi in lavorazione, questo comporta un basso WIP che influisce sugli investimenti da sostenere in materie prime e semilavorati.
Basso WIP e riduzione dei costi influiscono anche sul flow time che viene ridotto a sua volta.
Il beneficio fondamentale offerto da questa tecnica è il controllo costante del livello produttivo della linea, nessun ordine viene messo in lavorazione senza che la capacità effettiva non lo consenta.
Si evitano pertanto errori di gestione ed eventuali colli di bottiglia.
Soluzioni ibride kanban-CONWIP
Sempre più spesso viene presa in considerazione l’unione dei due sistemi sfruttando i reciproci punti di forza.
Quando si devono gestire sia lavorazioni constanti che su richiesta, vengono messe in coda sia le carte kanban che CONWIP.
Le prime non appena arrivano a monte della linea produttiva, innescano la produzione dei numeri di parte alle quali corrispondono, le seconde invece mettono in lavorazione le parti più urgenti del backlog composto da quelle su ordinazione e a basso volume.
Questa versione ibrida sfrutta appieno i vantaggi di entrambi i sistemi per controllare una produzione di più ampia gestione.
La seconda versione ibrida prevederebbe l’associazione di due carte a ciascuna parte, una CONWIP e una Kanban.
In questa tipologia di sistema CONWIP ha un loop grande e kanban più loop in sequenza.
Questa soluzione prevede più lavoro e conseguente rischio di errore, per questa ragione se si decide d'intraprendere questa strada, sarebbe consigliabile valutare se i vantaggi sono sufficienti per compensare il rischio.
Sia il sistema CONWIP che kanban sono sistemi pull dalle grandi possibilità, per questo ti consiglio di analizzare attentamente il tuo flusso di lavoro e capire quale riuscirebbe a offrirti i benefici maggiori in termini di efficienza e organizzazione.
Come applicare il metodo CONWIP
All'interno di un'azienda c'è bisogno d'implementare un flusso produttivo eliminando improvvisazione e spostamenti inutili: ogni passaggio prevede un movimento dedicato a un'azione. Questo avviene grazie a una serie di strumenti come il porta kanban per consentire l'applicazione e la protezione del cartellino al materiale, la Lavagna kanban per la gestione visiva della produzione e i contenitori VDA KLT, fondamentali per la movimentazione delle parti lungo la linea di montaggio.
Vuoi maggiori informazioni? Per ulteriori domande e per scoprire come applicare il principio del metodo kanban alla tua azienda, contattaci all’indirizzo e-mail info@utekvision.com!