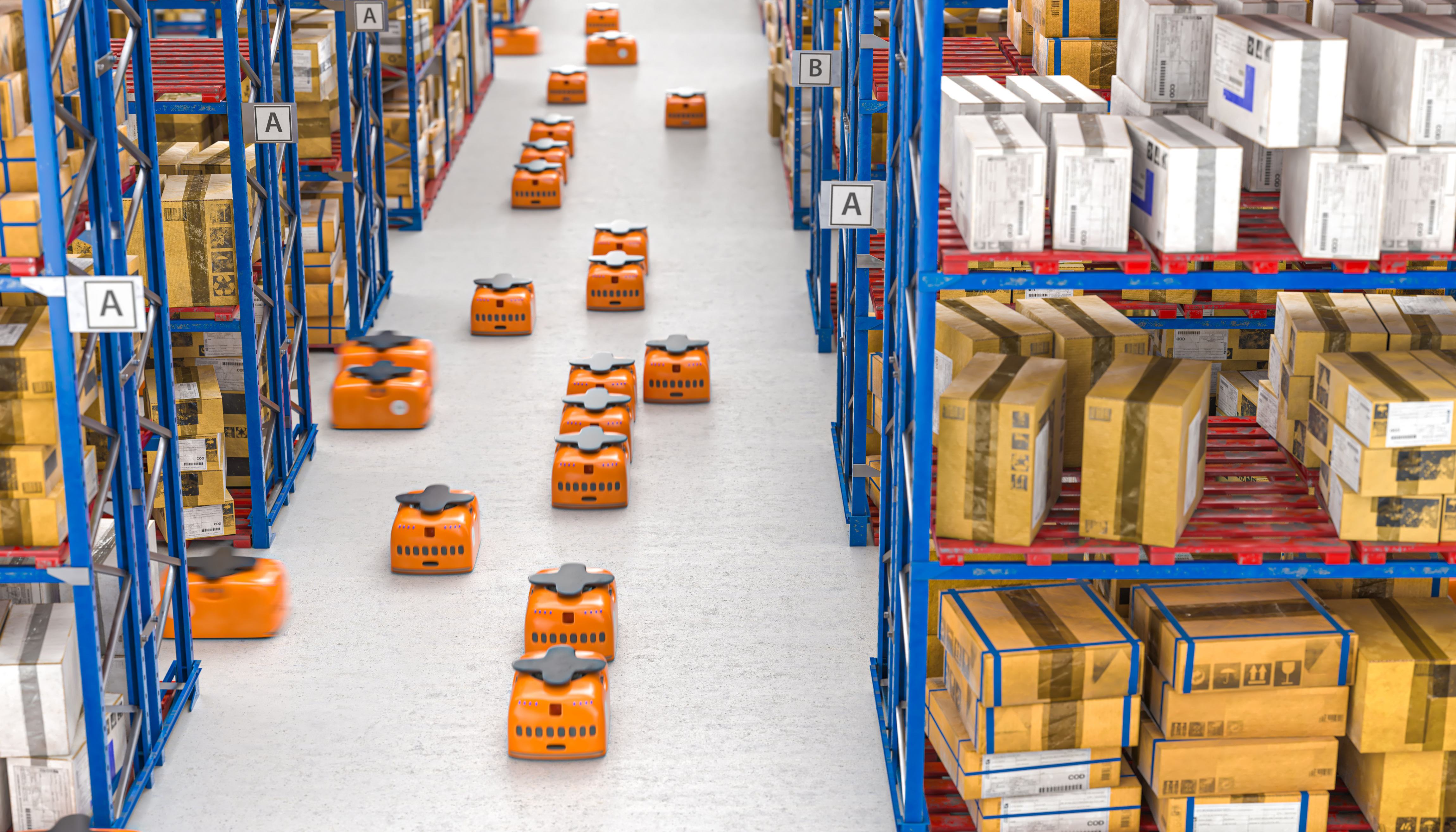
Indice dei contenuti
Uno dei dubbi fondamentali per chi vuole snellire il processo interno della propria attività, come organizzare un magazzino da zero? Capita, spesso, di trovarsi in questa condizione che per molti può essere un problema, una perdita di tempo. Chi ragiona in termini di Lean Transformation sa che deve cogliere al volo. Perché un magazzino gestito bene migliora il processo operativo.
Con la crescita del mercato globale, i magazzini sono costantemente sotto pressione per prestazioni migliori, più veloci ed efficienti. Con l'aumentare di questa pressione, il ruolo della gestione Lean del magazzino diventa sempre più rilevante. Utilizzando i principi del Lean Manufacturing, i magazzini vedranno un notevole miglioramento nel organizzazione, e nel flusso dei prodotti, nonché nella capacità di soddisfare le esigenze del cliente.
Che cos è il magazzino?
I magazzini moderni non sono limitati allo stoccaggio. Dato che le loro operazioni includono processi come la ricezione, l'immagazzinamento, la raccolta, l'imballaggio e la spedizione, ecc... La metodologia Lean viene applicata anche al magazzino.
Nel contesto del magazzino, devi eliminare tutti i processi e attività che assorbono risorse senza creare alcun valore aggiunto ("Muda").
In particolar modo si traduce in minor perdita di tempo nella elaborazione degli ordini, riduzione dei costi operativi, trasporti superflui, infortuni ridotti, ottimizzazione degli spazi e miglioramento delle performance di chi opera in quest' area.
Detto in altre parole, prendiamo per buone i temi che si trovano alla base della Lean Manufacturing: riduciamo eccesso di attività, scorte, attese e movimento.
Come organizzare un magazzino da zero? Iniziamo dalle basi della Lean Organization per lavorare meglio, ma soprattutto subito.
Qual è il flusso di lavoro di magazzino?
Per capire bene come organizzare un magazzino da zero bisogna riflettere sul processo che investe questo spazio. La merce arriva, si registra e posiziona sugli scaffali. Da qui viene presa, portata verso l’imballaggio e poi spedita (se si tratta di un'azienda commerciale). Potrebbero esserci tante differenze in questa catena di eventi. Ad esempio, di che merce si tratta?
Stiamo parlando di materie prime non lavorate? Arrivano carichi pesanti che devono essere spostati con un carrello elevatore? Magari c’è bisogno di un’area riservata per mantenere il tutto in sicurezza?
Lavora sulla sequenza delle operazioni avendo come punto di riferimento le azioni che devono fare i lavoratori e le macchine all’interno degli spazi. Per fare questo hai bisogno di un analisi della catena del valore mappando graficamente tutti i processi e le attività necessarie per la realizzazione di un prodotto, partendo dal fornitore fino alla consegna del finito. Questa Mappatura della catena del valore si chiama VSM dal acronimo "Value Stream Mapping".
La mappatura del flusso è un processo che ti consente di capire come funzionano le cose. Il flusso di lavoro è mappato visivamente e le relazioni tra i processi sono chiaramente identificate, consentendoti di:
- Comprendere come interagiscono i vari processi.
- Scoprire come la pianificazione e il flusso di lavoro dipartimentale influiscono sulle operazioni.
- Identificare potenziali lacune nei processi.
Creando una mappa visiva, potrai identificare i materiali che vengono immagazzinati in modo inefficace e gestiti non correttamente. Puoi anche migliorare il layout del magazzino e il sistema di stoccaggio per ridurre la gestione e migliorarne la modalità di conservazione degli articoli.
Quali sono gli spostamenti da organizzare in magazzino?
Riflettere sul flusso che porta un magazzino a riempirsi con la merce o le materie prime necessarie permette di gestire uno degli aspetti più importanti in termini di Lean Organization, identificare le attività a valore aggiunto e non. Qual è il valore? Come riconosco le attività a valore aggiunto?
Il valore può essere semplicemente definito come qualcosa che un cliente è disposto a pagare per ricevere, se non è disposto a pagarlo, non ha valore.
Stiamo parlando degli sprechi. Il principio chiave è semplice: qualunque cosa o chiunque non aggiunga valore è uno spreco. Bisogna eliminare gli sprechi per ridurre i costi delle attività necessarie.
Per i principi del Lean Manufacturing le attività non a valore aggiunto si dividono in sette sprechi:
- Tempi di attesa, il tempo d'inattività in cui chi potrebbe fare qualcosa, non sta facendo nulla. Tuttavia, ci sono numerose opportunità di miglioramento del tempo di attesa ad esempio utilizzando sistemi di sollevamento e tecnologie di movimentazione materiali.
- Movimenti inutili, si riferisce a raggiungere materiali e attrezzature lontane dal punto di utilizzo. Organizza le aree di lavoro con solo le attrezzature e i materiali che servono implementando Flow-Rack, carrelli Kitting e Workstation Ergonomiche.
- Scorte, sono un costo per spazio di stoccaggio e per le tasse! Scorte in eccesso inoltre aumentano il rischio di deterioramento e obsolescenza dei prodotti. Gestisci le scorte con la filosofia Just In Time!
- Eccesso di attività, non impiegare più operazioni di quanto sia necessario per il cliente finale. Il lavoro extra non ha valore!
- Sovrapproduzione, significa produrre più di quanto sia necessario. L'eccesso di produzione si traduce in elevati costi di magazzino. La soluzione è passare dalla tecnica Push a quella Pull!
- Difetti, i prodotti difettosi devono essere eliminati o rilavorati. Ci sono metodi Lean come il Poka-Yoke, efficaci nel eliminare errori di produzione, KO e difetti, portando risparmi ancora maggiori.
- Trasporto, ogni movimento del materiale non crea valore. Ottimizza i processi mappando correttamente i flussi realizzando una Value Stream Mapping.
L'uso corretto di strumenti di comunicazione visiva Visual Management ti aiutano a ridurre ed eliminare gli sprechi:
- Comunicare procedure operative nel punto e nel momento necessario.
- Fornire indicazioni, guidando le persone e i lavoratori in sicurezza.
- Identificare le posizioni delle attrezzature di sicurezza e di produzione.
Come organizzare gli spazi all’interno del magazzino?
Andiamo al nocciolo della questione. Stai lottando su come organizzare gli spazi nel tuo magazzino in modo più efficiente? Tieni in considerazione le seguenti idee e suggerimenti sull'organizzazione del magazzino.
- Rivaluta il tuo layout, si consiglia di effettuare questa valutazione ogni quattro o cinque anni, in base al tasso di crescita della tua azienda. Naturalmente i requisiti di spazio nel tuo magazzino dovranno essere rivisti nel tempo.
- Magazzino dinamico, i prodotti a maggiore rotazione probabilmente cambieranno con le stagioni, quindi riadatta il magazzino in base alla frequenza di picking una volta all'anno. Il tuo sistema di gestione del magazzino WMS dovrebbe avere un modulo dinamico di posizione.
- Massimizza lo spazio disponibile, invece di un'espansione della metratura considera un migliore utilizzo dello spazio verticale. Non gestire piccole parti su scaffalature pallet, sprechi spazio e favoriresti errori di posizionamento, magazzini dinamici e flow-rack sono la soluzione. Utilizza contenitori standardizzati per mantenere gli scaffali ordinati.
Quindi, come organizzare il magazzino da zero? Occupando meno spazio possibile con la merce in stoccaggio, in modo intelligente. Questo significa scegliere e organizzare gli scaffali seguendo i principi del pensiero legato al Lean Manufacturing. Un esempio concreto?
Impostare le attività secondo la logica pull e non push, ovvero realizzare un'attività solo quando il processo a valle lo richieda.
Questa è la definizione di Wikipedia che prende in considerazione un aspetto importante da riprodurre nel magazzino: pensare a come organizzare meglio gli spazi pensando a non dover trovare posto per scorte infinite ma ridurre la necessità di avere tanto in magazzino e puntare soprattutto sull’efficienza e la velocità dei movimenti. A tal proposito leggi il prossimo paragrafo, è decisivo per il tuo lavoro
Come velocizzare le tue operazioni?
Il tuo magazzino è piccolo o grande? La quantità di tempo speso nella raccolta ordini è una buona parte dei costi. Se il magazzino è organizzato in modo efficiente, è possibile sequenziare gli ordini raggruppandoli per percorso di prelievo o aree all'interno del magazzino. Non dimenticare di assegnare le posizioni dei prodotti in base alla regola 80/20. Il 20% dei prodotti rappresenta l'80% del attività di prelievo. I prodotti con più alta frequenza di prelievo devono essere stoccati vicino alle stazioni di spedizione o alle aree per operazioni secondarie.
Riduci i tempi di viaggio, migliorando la produttività del commissionamento. Per questo motivo le aziende investono sui sistemi di trasporto e movimentazione dei carichi:
La comunicazione visiva è un elemento chiave per qualsiasi magazzino Lean. Utilizza etichette e cartelli per identificare le scaffalature del magazzino e fornire informazioni importanti, mentre la marcatura del pavimento per delineare percorsi separati per pedoni e muletti, guidando i lavoratori e visitatori in sicurezza verso le loro destinazioni. Inoltre puoi delimitare aree riservate o non sicure, contrassegnare spazi designati al parcheggio e ricarica dei carrelli elevatori. Questo crea una mappa visiva che aiuta i lavoratori a orientarsi in magazzino.
Come puoi rendere un magazzino sicuro?
Chi organizza un magazzino deve assicurarsi di rispettare le norme di sicurezza obbligatorie.
Inutile dire quanto sia fondamentale quest’aspetto per le persone che ci lavorano e l’azienda che sovrintende alle operazioni, il rispetto di tali norme ti consente di evitare controversie prevenendo incidenti e infortuni.
Come garantire la sicurezza:
- Effettua una valutazione del rischio con intervalli regolari adottando un piano di sicurezza
- Revisiona il layout e la progettazione del magazzino in un'ottica di sicurezza, inclusi fattori come passerelle, rampe / scale, scaffalature, vie di fuga, ecc...
- Utilizza la segnaletica orizzontale e i cartelli di sicurezza per la gestione del traffico e per segnalare aree pericolose come i bordi delle banchine di carico.
- Iscrivi il tuo personale addetto ai corsi sulla sicurezza.
- Assegna i dispositivi di protezione individuale DPI ai lavoratori e ai visitatori
- Crea un piano antincendio e di emergenza che includa uscite, porte tagliafuoco, procedure di evacuazione, posizione degli estintori e monitoraggio di tutti i visitatori presenti informandoli sul piano di sicurezza.
La sicurezza sul lavoro ha un altro benefit, la massima efficienza.
Un magazziniere che sa di lavorare in sicurezza è più concentrato sul compito e veloce nell’esecuzione.